Q&A: Melody Maas, Midion and Kevin Braziel, McGough
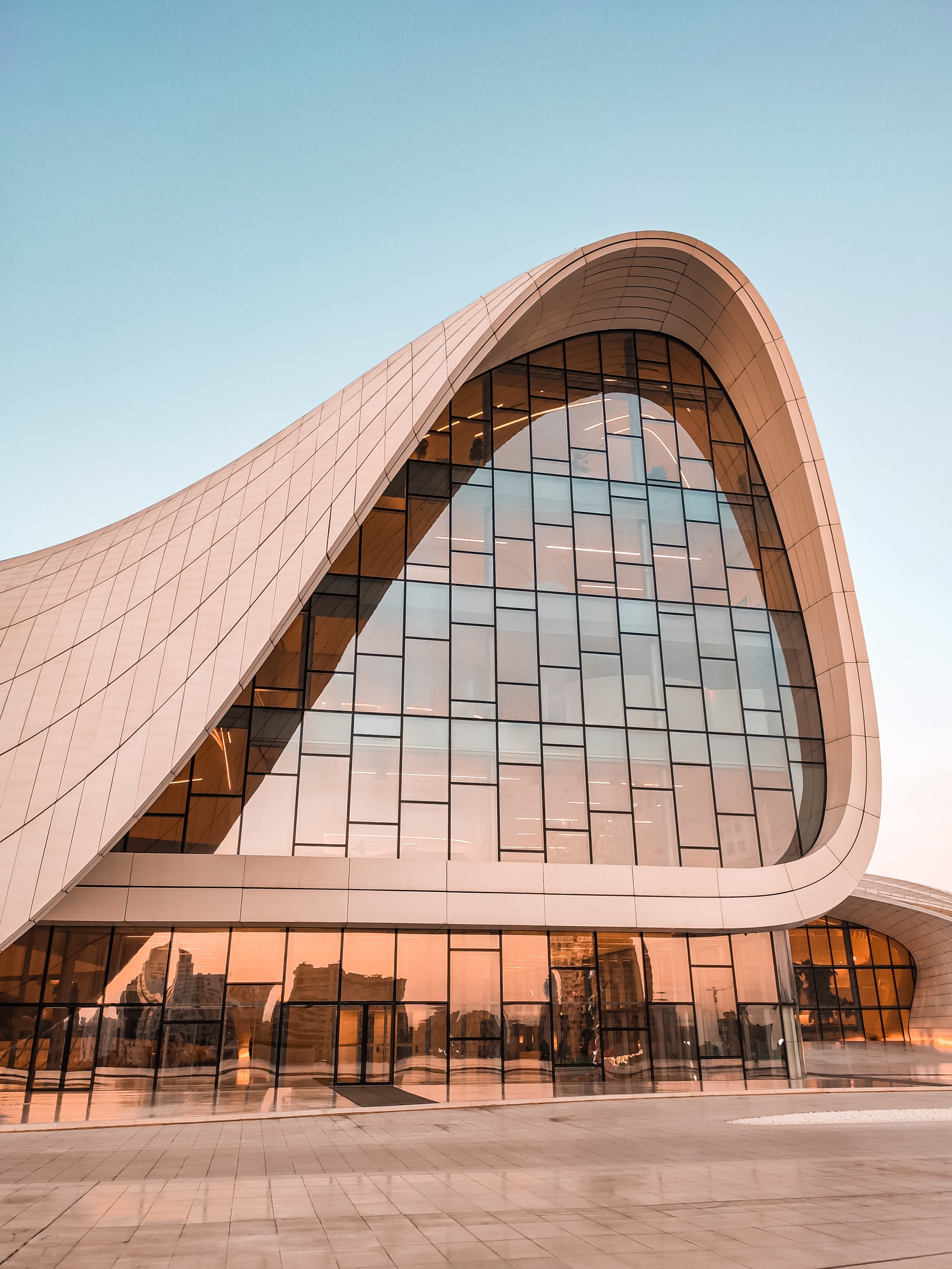
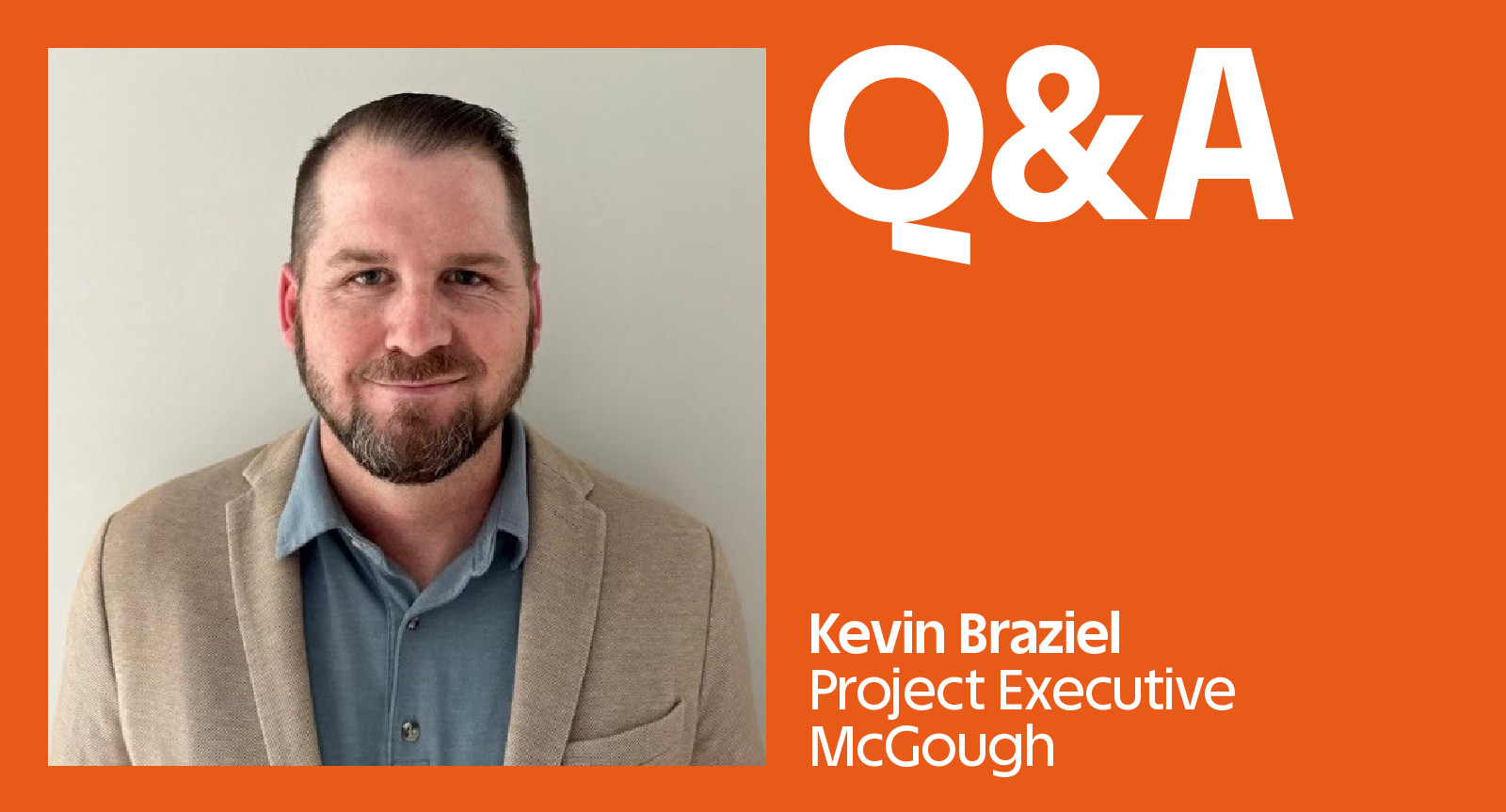
Background: Progressed from Project Manager to Project Executive across various general contractors, with experience in the pharmaceutical and life sciences sectors.
What was your familiarity with lean previously?
Quite a bit. I worked on a large project where the Last Planner System (LPS) was required as the primary planning tool by a previous general contractor.
What do you feel like the limits of lean are?
The biggest limitation is team dynamics. If your team isn’t aligned and fully bought into lean, it just becomes a set of pretty pictures on a wall—more of a conversation piece than a practical tool.
At a previous GC, there was a mandate to practice lean principles, but it wasn’t clearly defined. It turned into a check-the-box exercise. A dedicated group was tasked with implementing lean, but they ended up going through the motions without meaningful outcomes.
No one was learning anything, which completely devalued the process. If we’d continued on that path, all 27 team members would have dismissed lean entirely in future projects. If your team doesn’t understand or believe in its importance, don’t even bother.
How have you experienced Midion going beyond lean construction?
Midion has elevated the approach by emphasizing team building—through workshops, individual and team coaching, communication strategies, and events like LEGO Serious Play.
I can’t stress enough how crucial team dynamics are. I’ve told my current team they need to be all in—or not in at all. Bringing in Midion as a consultant focused on team cohesion helped to ensure everyone understands the process and commits fully.
What advice do you have for other leaders looking to grow beyond lean?
If your team isn’t functioning as a cohesive unit, don’t even think about implementing lean. Focus on building the team first!
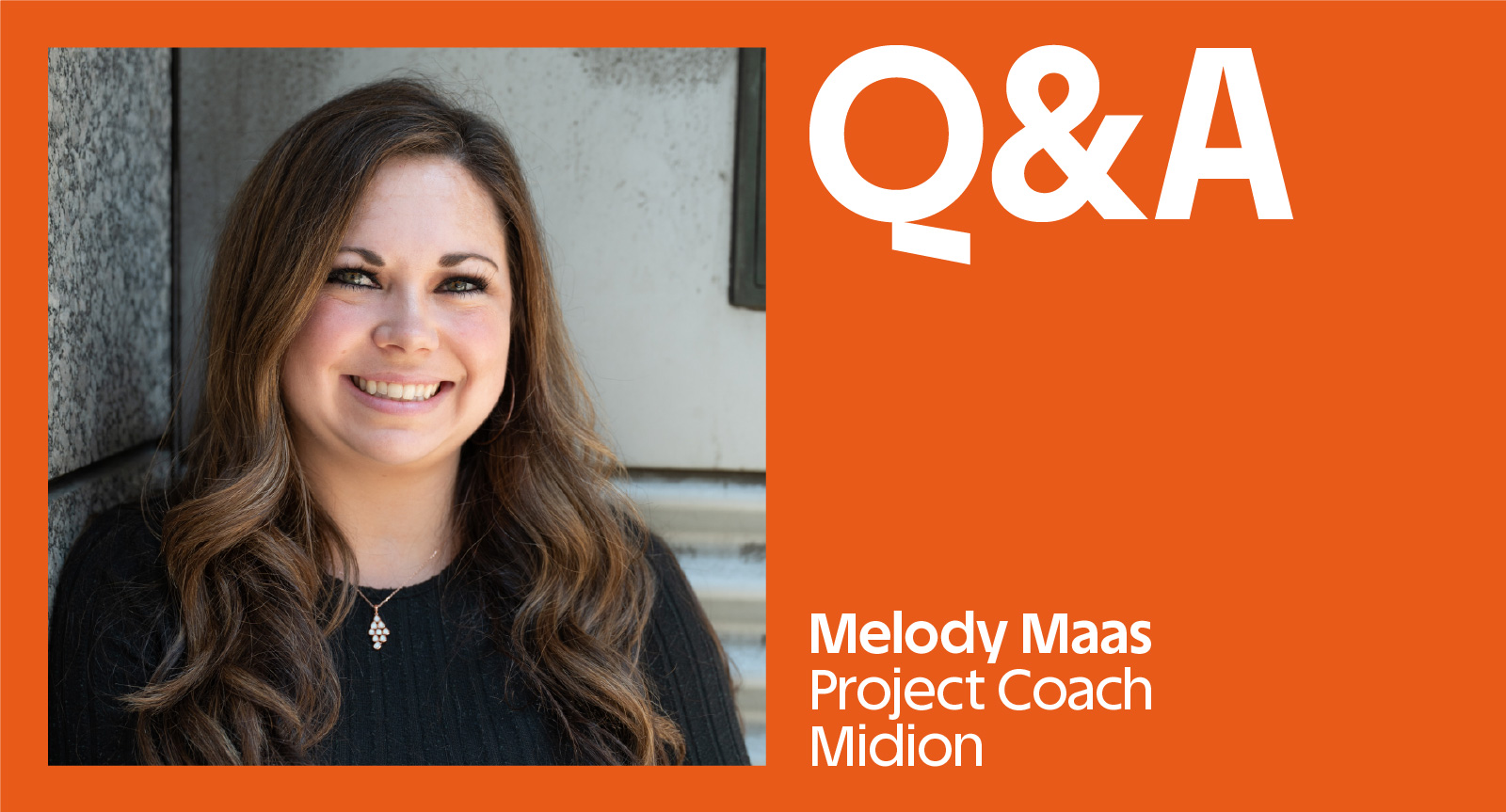
Background: Started out as a chemical engineer, then moved into construction. Progressed from Project Engineer to Assistant Project Manager for a global general contractor on semiconductor projects.
What was your familiarity with lean prior to Midion?
When I first got into construction, the general contractor I worked for was already using lean practices like the Last Planner System—things like Weekly Work Plans and Pull Planning were just part of how we operated.
Before that, I studied chemical engineering, which is also known as process engineering. We were always looking for ways to simplify systems and reduce waste in our experiments and production, so in a way, I was already thinking lean before I even knew what it was in a construction context.
What do you feel like the limits of lean are?
Lean is effective when everyone’s on board and trained well. But even with the perfect process, the project can still fall apart if the team’s not aligned.
Lean focuses on streamlining production and cutting out waste, but it doesn’t always account for the human side of construction—the personalities, the communication styles, the constant changes. If the team isn’t all moving in the same direction, lean won’t save the project.
How have you experienced Midion going beyond lean construction?
What really makes a difference at Midion is the focus on people. The coaching, workshops, and communication tools we use have a huge impact—not just on the project, but on people’s careers.
One of the first things we do with a team is figure out everyone’s Enneagram type. It helps people understand themselves and each other—how they show up, what their strengths are, where they might need support. Then we help individuals recognize the strengths and weaknesses of their type to identify where to put their efforts; whether that be being the go-to person for a certain task, growing confidence in weaker areas, or being comfortable to ask someone for help that has a clear strength in an area.
When leadership is part of that process (which is key), it sets the tone for the whole team. That’s when lean tools like the Last Planner System actually stick—because the team’s communicating openly and working as one unit.
If we’d skipped all of that and just jumped into LPS, there’s no way we’d have open communication while planning work. You have to build the trust and connection first.
What advice do you have for other leaders looking to grow beyond lean?
Start with relationships. Construction is full of tough personalities and high pressure situations, so your project team needs to be a place where people feel safe and supported.
Sometimes that shift happens naturally when a few peer leaders step up, but it works significantly better when leadership is intentional about it from the start.
And if you’re someone who sees the value in going beyond lean but isn’t sure where to start—Midion’s here for that. We’re all about helping teams work better and move the project forward by focusing on the people first.
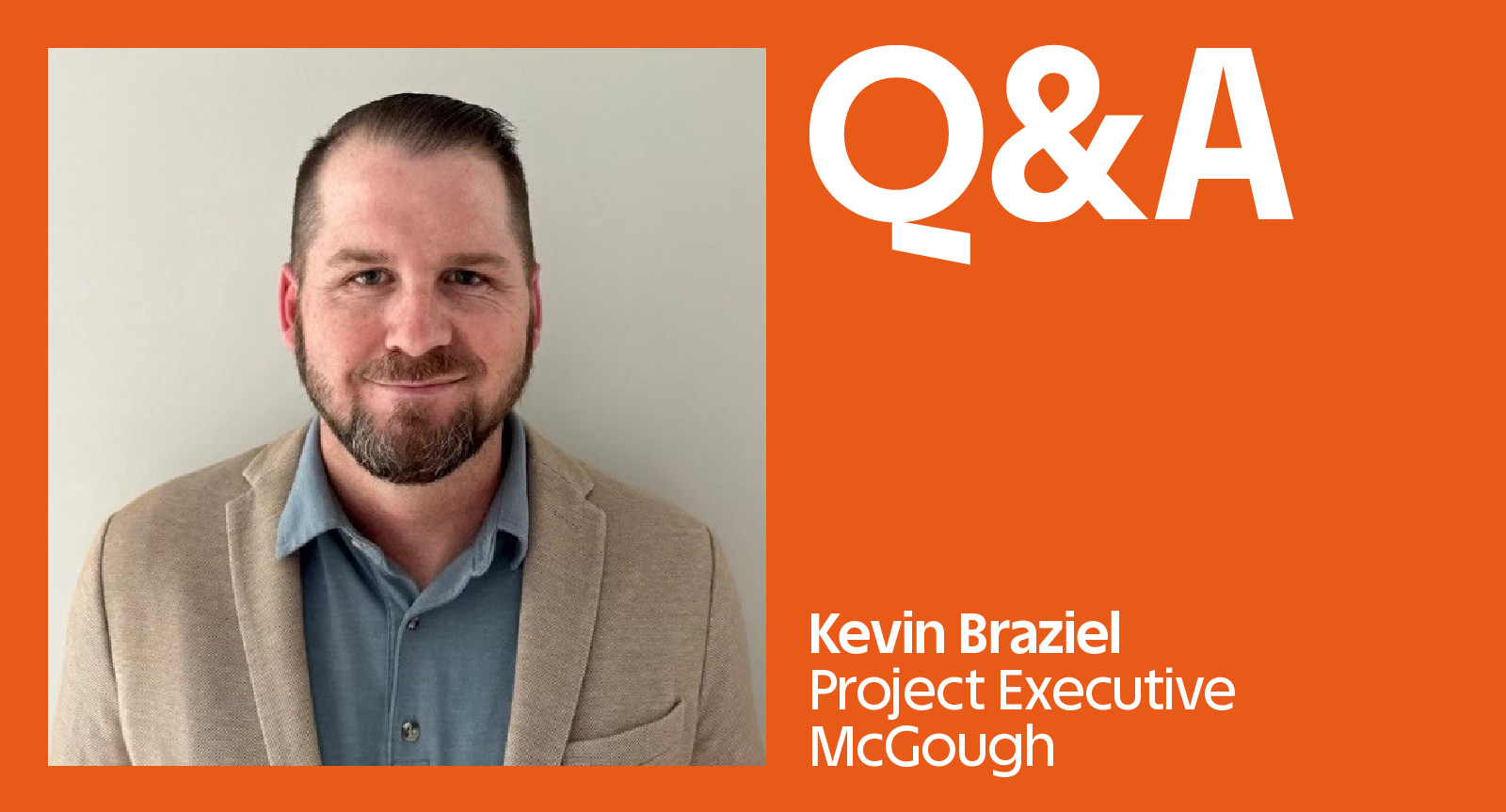
Background: Progressed from Project Manager to Project Executive across various general contractors, with experience in the pharmaceutical and life sciences sectors.
What was your familiarity with lean previously?
Quite a bit. I worked on a large project where the Last Planner System (LPS) was required as the primary planning tool by a previous general contractor.
What do you feel like the limits of lean are?
The biggest limitation is team dynamics. If your team isn’t aligned and fully bought into lean, it just becomes a set of pretty pictures on a wall—more of a conversation piece than a practical tool.
At a previous GC, there was a mandate to practice lean principles, but it wasn’t clearly defined. It turned into a check-the-box exercise. A dedicated group was tasked with implementing lean, but they ended up going through the motions without meaningful outcomes.
No one was learning anything, which completely devalued the process. If we’d continued on that path, all 27 team members would have dismissed lean entirely in future projects. If your team doesn’t understand or believe in its importance, don’t even bother.
How have you experienced Midion going beyond lean construction?
Midion has elevated the approach by emphasizing team building—through workshops, individual and team coaching, communication strategies, and events like LEGO Serious Play.
I can’t stress enough how crucial team dynamics are. I’ve told my current team they need to be all in—or not in at all. Bringing in Midion as a consultant focused on team cohesion helped to ensure everyone understands the process and commits fully.
What advice do you have for other leaders looking to grow beyond lean?
If your team isn’t functioning as a cohesive unit, don’t even think about implementing lean. Focus on building the team first!
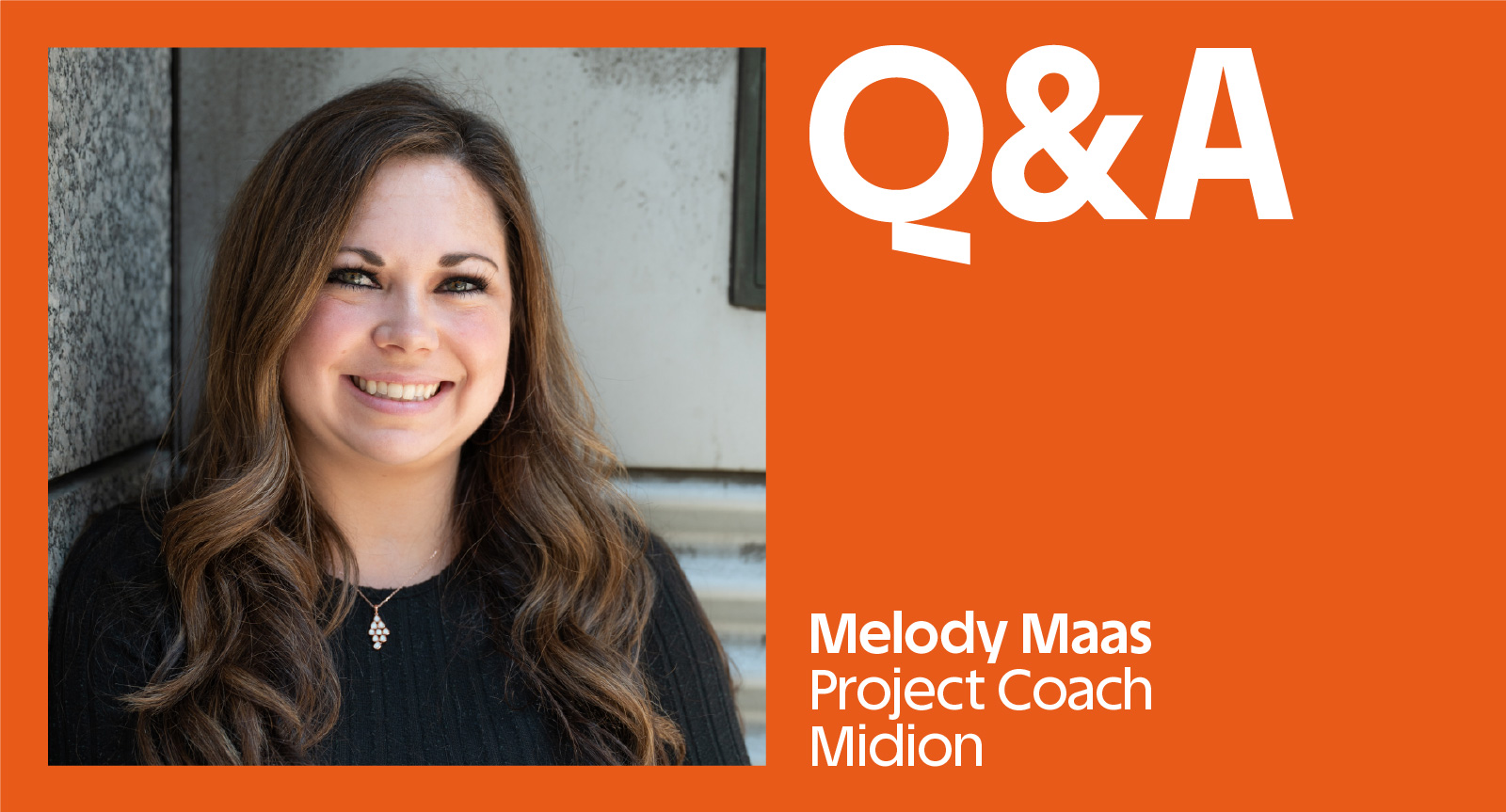
Background: Started out as a chemical engineer, then moved into construction. Progressed from Project Engineer to Assistant Project Manager for a global general contractor on semiconductor projects.
What was your familiarity with lean prior to Midion?
When I first got into construction, the general contractor I worked for was already using lean practices like the Last Planner System—things like Weekly Work Plans and Pull Planning were just part of how we operated.
Before that, I studied chemical engineering, which is also known as process engineering. We were always looking for ways to simplify systems and reduce waste in our experiments and production, so in a way, I was already thinking lean before I even knew what it was in a construction context.
What do you feel like the limits of lean are?
Lean is effective when everyone’s on board and trained well. But even with the perfect process, the project can still fall apart if the team’s not aligned.
Lean focuses on streamlining production and cutting out waste, but it doesn’t always account for the human side of construction—the personalities, the communication styles, the constant changes. If the team isn’t all moving in the same direction, lean won’t save the project.
How have you experienced Midion going beyond lean construction?
What really makes a difference at Midion is the focus on people. The coaching, workshops, and communication tools we use have a huge impact—not just on the project, but on people’s careers.
One of the first things we do with a team is figure out everyone’s Enneagram type. It helps people understand themselves and each other—how they show up, what their strengths are, where they might need support. Then we help individuals recognize the strengths and weaknesses of their type to identify where to put their efforts; whether that be being the go-to person for a certain task, growing confidence in weaker areas, or being comfortable to ask someone for help that has a clear strength in an area.
When leadership is part of that process (which is key), it sets the tone for the whole team. That’s when lean tools like the Last Planner System actually stick—because the team’s communicating openly and working as one unit.
If we’d skipped all of that and just jumped into LPS, there’s no way we’d have open communication while planning work. You have to build the trust and connection first.
What advice do you have for other leaders looking to grow beyond lean?
Start with relationships. Construction is full of tough personalities and high pressure situations, so your project team needs to be a place where people feel safe and supported.
Sometimes that shift happens naturally when a few peer leaders step up, but it works significantly better when leadership is intentional about it from the start.
And if you’re someone who sees the value in going beyond lean but isn’t sure where to start—Midion’s here for that. We’re all about helping teams work better and move the project forward by focusing on the people first.
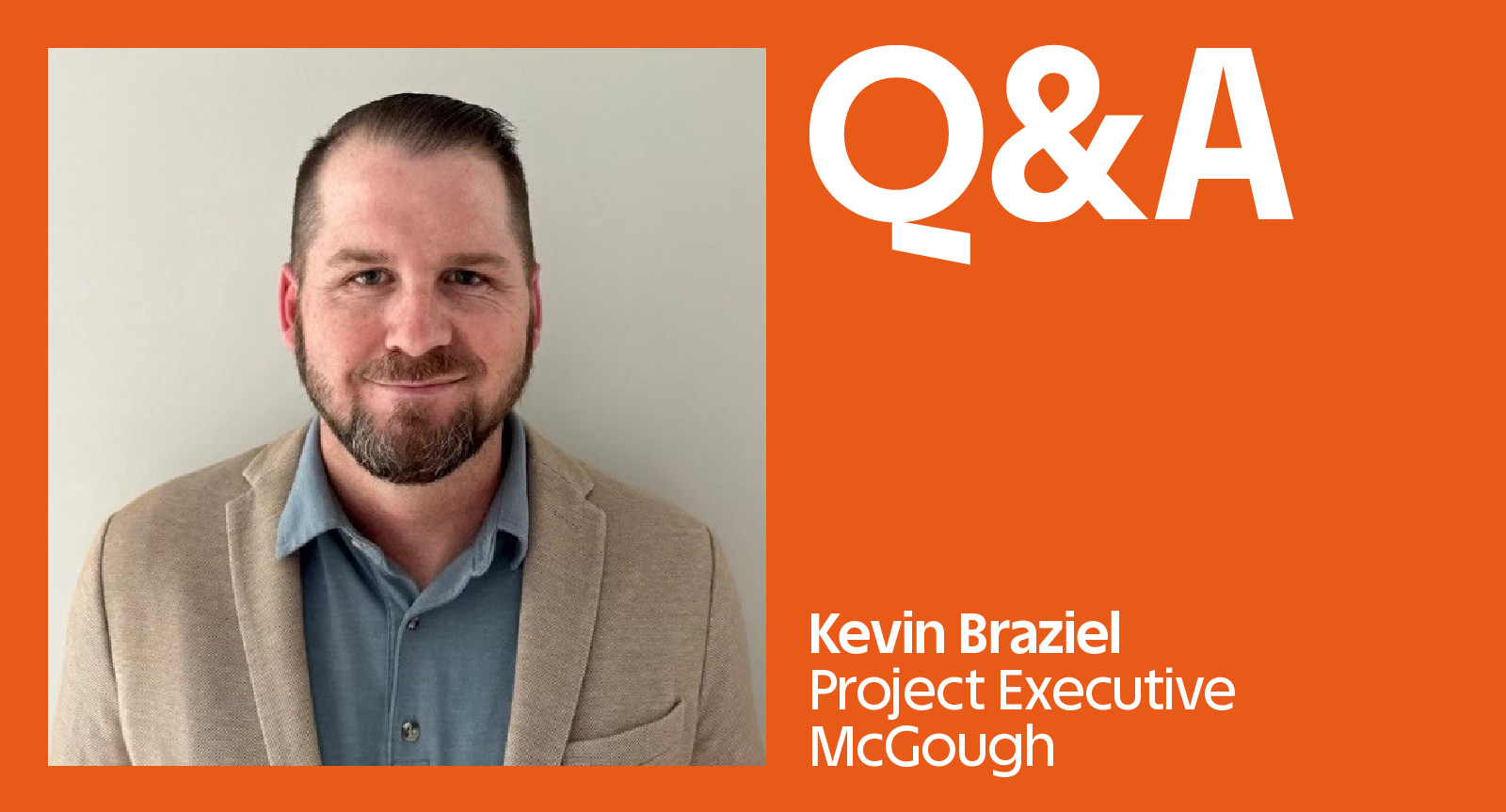
Background: Progressed from Project Manager to Project Executive across various general contractors, with experience in the pharmaceutical and life sciences sectors.
What was your familiarity with lean previously?
Quite a bit. I worked on a large project where the Last Planner System (LPS) was required as the primary planning tool by a previous general contractor.
What do you feel like the limits of lean are?
The biggest limitation is team dynamics. If your team isn’t aligned and fully bought into lean, it just becomes a set of pretty pictures on a wall—more of a conversation piece than a practical tool.
At a previous GC, there was a mandate to practice lean principles, but it wasn’t clearly defined. It turned into a check-the-box exercise. A dedicated group was tasked with implementing lean, but they ended up going through the motions without meaningful outcomes.
No one was learning anything, which completely devalued the process. If we’d continued on that path, all 27 team members would have dismissed lean entirely in future projects. If your team doesn’t understand or believe in its importance, don’t even bother.
How have you experienced Midion going beyond lean construction?
Midion has elevated the approach by emphasizing team building—through workshops, individual and team coaching, communication strategies, and events like LEGO Serious Play.
I can’t stress enough how crucial team dynamics are. I’ve told my current team they need to be all in—or not in at all. Bringing in Midion as a consultant focused on team cohesion helped to ensure everyone understands the process and commits fully.
What advice do you have for other leaders looking to grow beyond lean?
If your team isn’t functioning as a cohesive unit, don’t even think about implementing lean. Focus on building the team first!
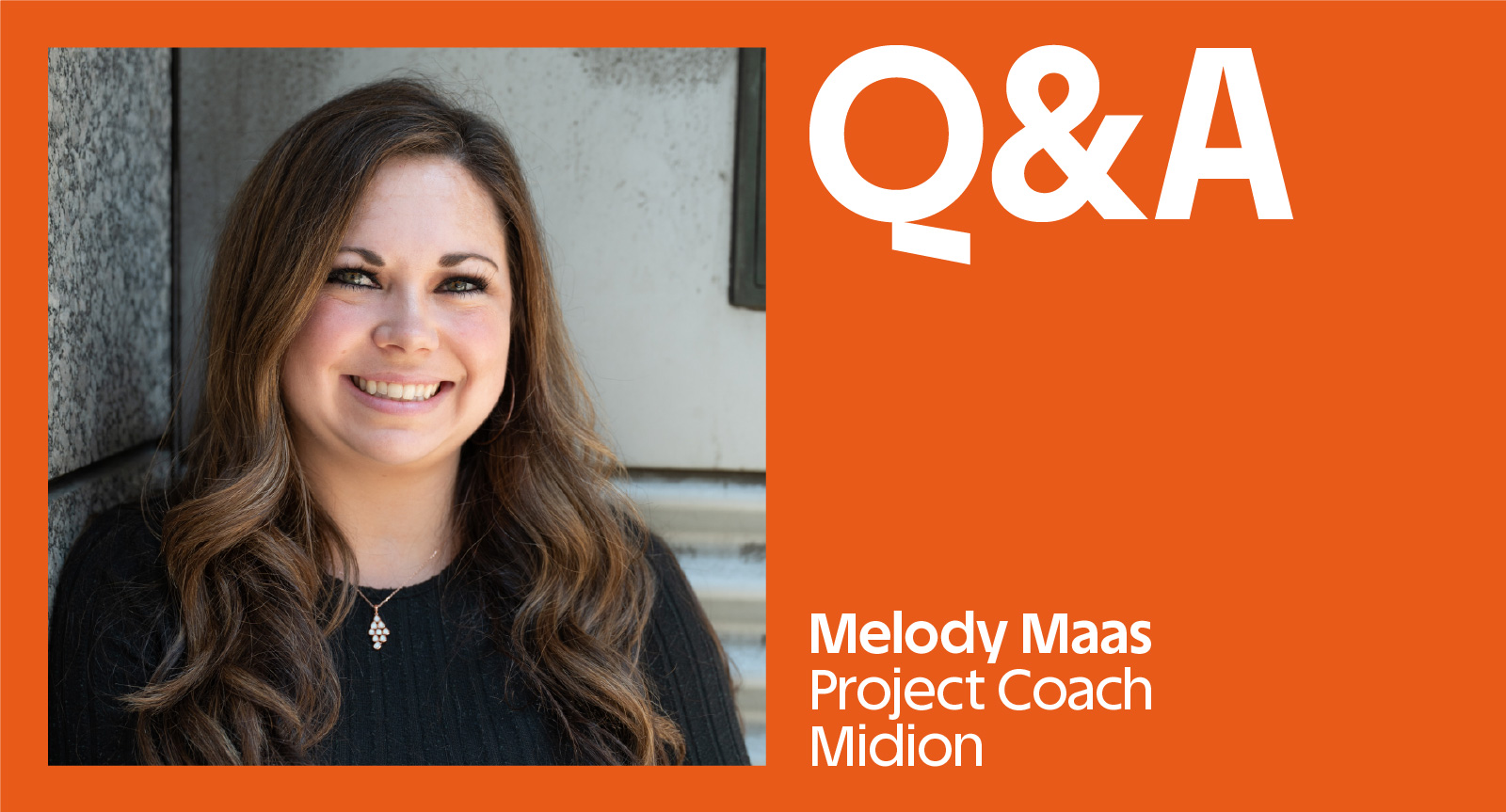
Background: Started out as a chemical engineer, then moved into construction. Progressed from Project Engineer to Assistant Project Manager for a global general contractor on semiconductor projects.
What was your familiarity with lean prior to Midion?
When I first got into construction, the general contractor I worked for was already using lean practices like the Last Planner System—things like Weekly Work Plans and Pull Planning were just part of how we operated.
Before that, I studied chemical engineering, which is also known as process engineering. We were always looking for ways to simplify systems and reduce waste in our experiments and production, so in a way, I was already thinking lean before I even knew what it was in a construction context.
What do you feel like the limits of lean are?
Lean is effective when everyone’s on board and trained well. But even with the perfect process, the project can still fall apart if the team’s not aligned.
Lean focuses on streamlining production and cutting out waste, but it doesn’t always account for the human side of construction—the personalities, the communication styles, the constant changes. If the team isn’t all moving in the same direction, lean won’t save the project.
How have you experienced Midion going beyond lean construction?
What really makes a difference at Midion is the focus on people. The coaching, workshops, and communication tools we use have a huge impact—not just on the project, but on people’s careers.
One of the first things we do with a team is figure out everyone’s Enneagram type. It helps people understand themselves and each other—how they show up, what their strengths are, where they might need support. Then we help individuals recognize the strengths and weaknesses of their type to identify where to put their efforts; whether that be being the go-to person for a certain task, growing confidence in weaker areas, or being comfortable to ask someone for help that has a clear strength in an area.
When leadership is part of that process (which is key), it sets the tone for the whole team. That’s when lean tools like the Last Planner System actually stick—because the team’s communicating openly and working as one unit.
If we’d skipped all of that and just jumped into LPS, there’s no way we’d have open communication while planning work. You have to build the trust and connection first.
What advice do you have for other leaders looking to grow beyond lean?
Start with relationships. Construction is full of tough personalities and high pressure situations, so your project team needs to be a place where people feel safe and supported.
Sometimes that shift happens naturally when a few peer leaders step up, but it works significantly better when leadership is intentional about it from the start.
And if you’re someone who sees the value in going beyond lean but isn’t sure where to start—Midion’s here for that. We’re all about helping teams work better and move the project forward by focusing on the people first.
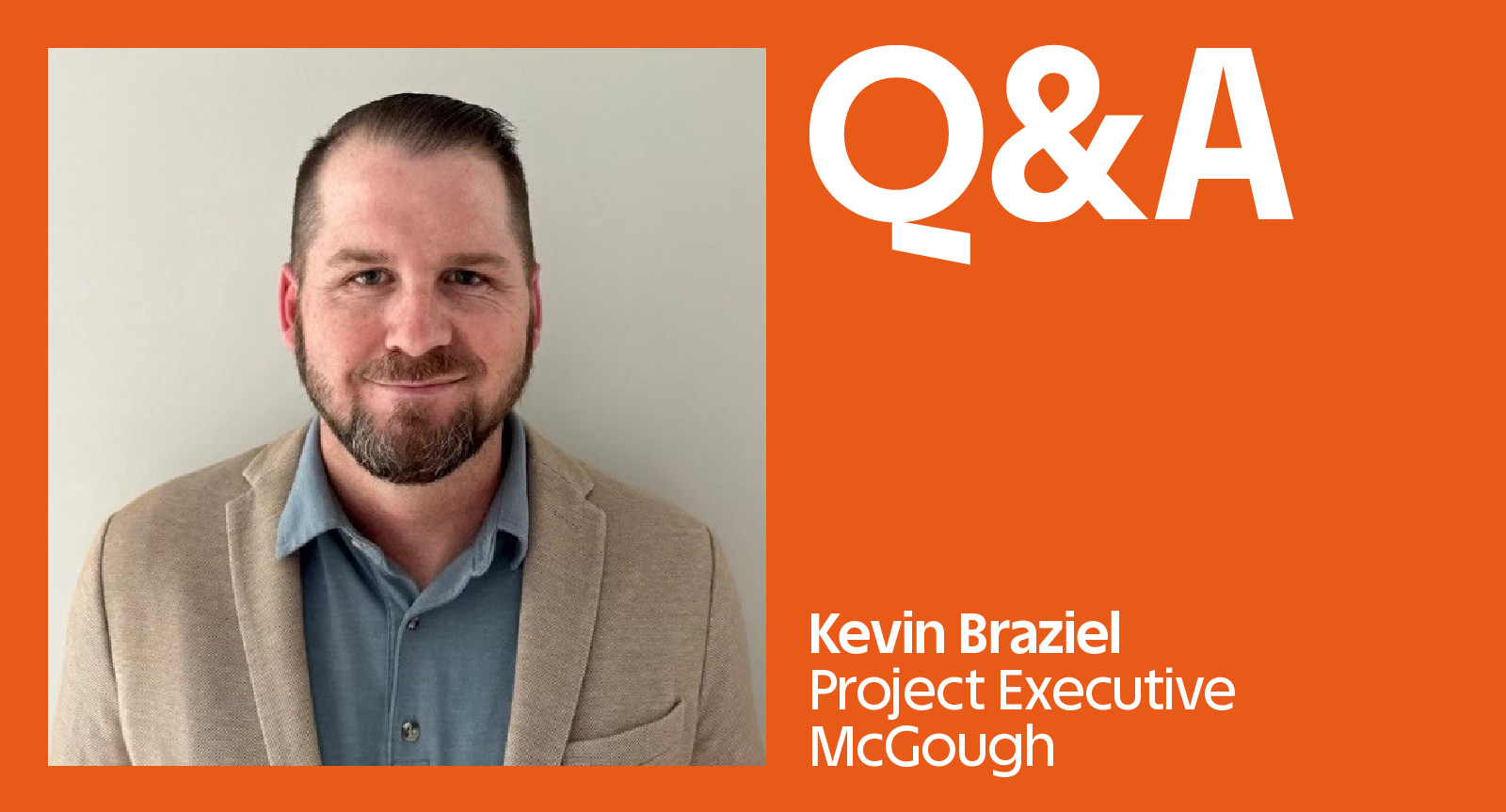
Background: Progressed from Project Manager to Project Executive across various general contractors, with experience in the pharmaceutical and life sciences sectors.
What was your familiarity with lean previously?
Quite a bit. I worked on a large project where the Last Planner System (LPS) was required as the primary planning tool by a previous general contractor.
What do you feel like the limits of lean are?
The biggest limitation is team dynamics. If your team isn’t aligned and fully bought into lean, it just becomes a set of pretty pictures on a wall—more of a conversation piece than a practical tool.
At a previous GC, there was a mandate to practice lean principles, but it wasn’t clearly defined. It turned into a check-the-box exercise. A dedicated group was tasked with implementing lean, but they ended up going through the motions without meaningful outcomes.
No one was learning anything, which completely devalued the process. If we’d continued on that path, all 27 team members would have dismissed lean entirely in future projects. If your team doesn’t understand or believe in its importance, don’t even bother.
How have you experienced Midion going beyond lean construction?
Midion has elevated the approach by emphasizing team building—through workshops, individual and team coaching, communication strategies, and events like LEGO Serious Play.
I can’t stress enough how crucial team dynamics are. I’ve told my current team they need to be all in—or not in at all. Bringing in Midion as a consultant focused on team cohesion helped to ensure everyone understands the process and commits fully.
What advice do you have for other leaders looking to grow beyond lean?
If your team isn’t functioning as a cohesive unit, don’t even think about implementing lean. Focus on building the team first!
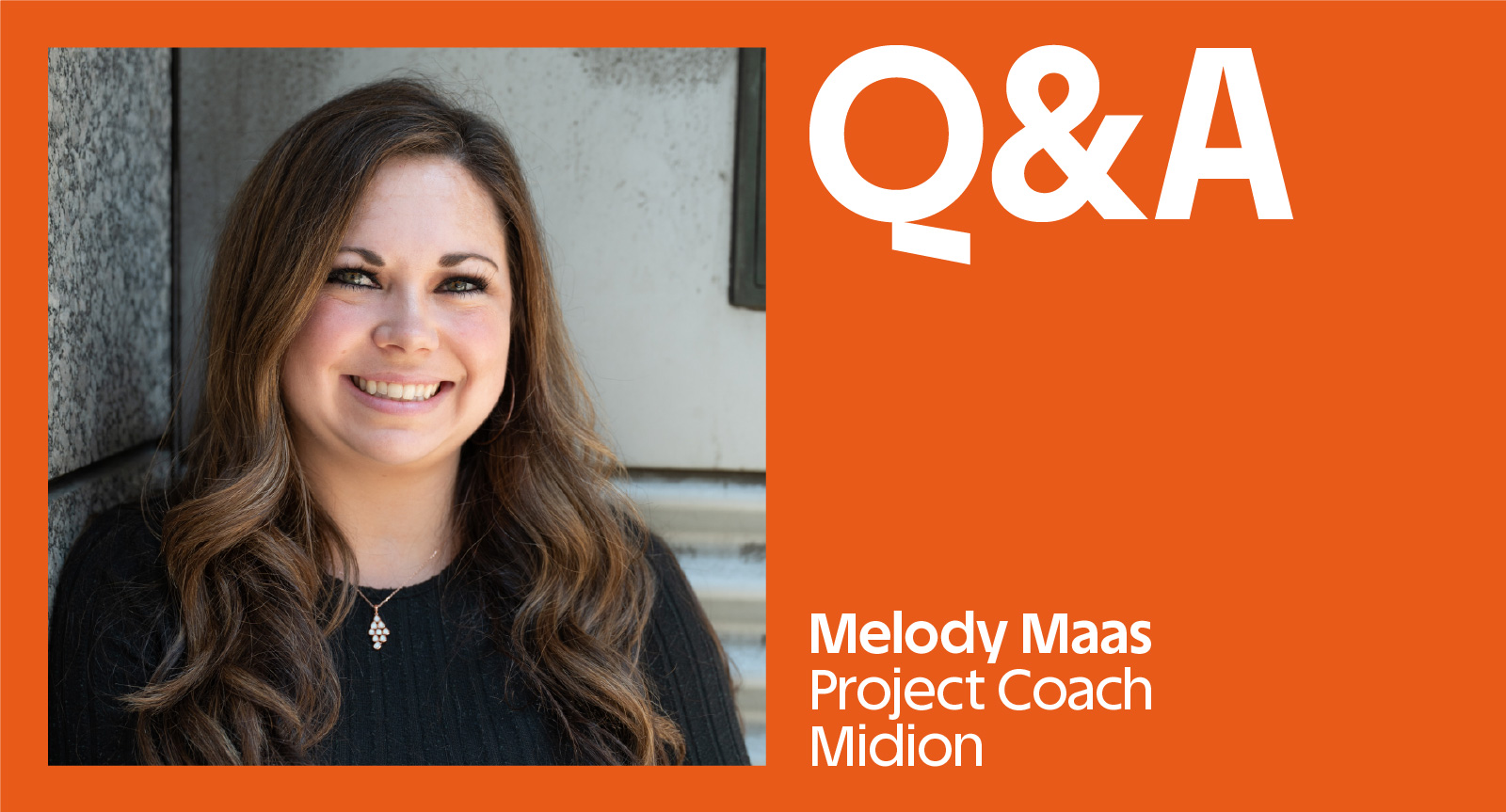
Background: Started out as a chemical engineer, then moved into construction. Progressed from Project Engineer to Assistant Project Manager for a global general contractor on semiconductor projects.
What was your familiarity with lean prior to Midion?
When I first got into construction, the general contractor I worked for was already using lean practices like the Last Planner System—things like Weekly Work Plans and Pull Planning were just part of how we operated.
Before that, I studied chemical engineering, which is also known as process engineering. We were always looking for ways to simplify systems and reduce waste in our experiments and production, so in a way, I was already thinking lean before I even knew what it was in a construction context.
What do you feel like the limits of lean are?
Lean is effective when everyone’s on board and trained well. But even with the perfect process, the project can still fall apart if the team’s not aligned.
Lean focuses on streamlining production and cutting out waste, but it doesn’t always account for the human side of construction—the personalities, the communication styles, the constant changes. If the team isn’t all moving in the same direction, lean won’t save the project.
How have you experienced Midion going beyond lean construction?
What really makes a difference at Midion is the focus on people. The coaching, workshops, and communication tools we use have a huge impact—not just on the project, but on people’s careers.
One of the first things we do with a team is figure out everyone’s Enneagram type. It helps people understand themselves and each other—how they show up, what their strengths are, where they might need support. Then we help individuals recognize the strengths and weaknesses of their type to identify where to put their efforts; whether that be being the go-to person for a certain task, growing confidence in weaker areas, or being comfortable to ask someone for help that has a clear strength in an area.
When leadership is part of that process (which is key), it sets the tone for the whole team. That’s when lean tools like the Last Planner System actually stick—because the team’s communicating openly and working as one unit.
If we’d skipped all of that and just jumped into LPS, there’s no way we’d have open communication while planning work. You have to build the trust and connection first.
What advice do you have for other leaders looking to grow beyond lean?
Start with relationships. Construction is full of tough personalities and high pressure situations, so your project team needs to be a place where people feel safe and supported.
Sometimes that shift happens naturally when a few peer leaders step up, but it works significantly better when leadership is intentional about it from the start.
And if you’re someone who sees the value in going beyond lean but isn’t sure where to start—Midion’s here for that. We’re all about helping teams work better and move the project forward by focusing on the people first.
Q&A: Melody Maas, Midion and Kevin Braziel, McGough
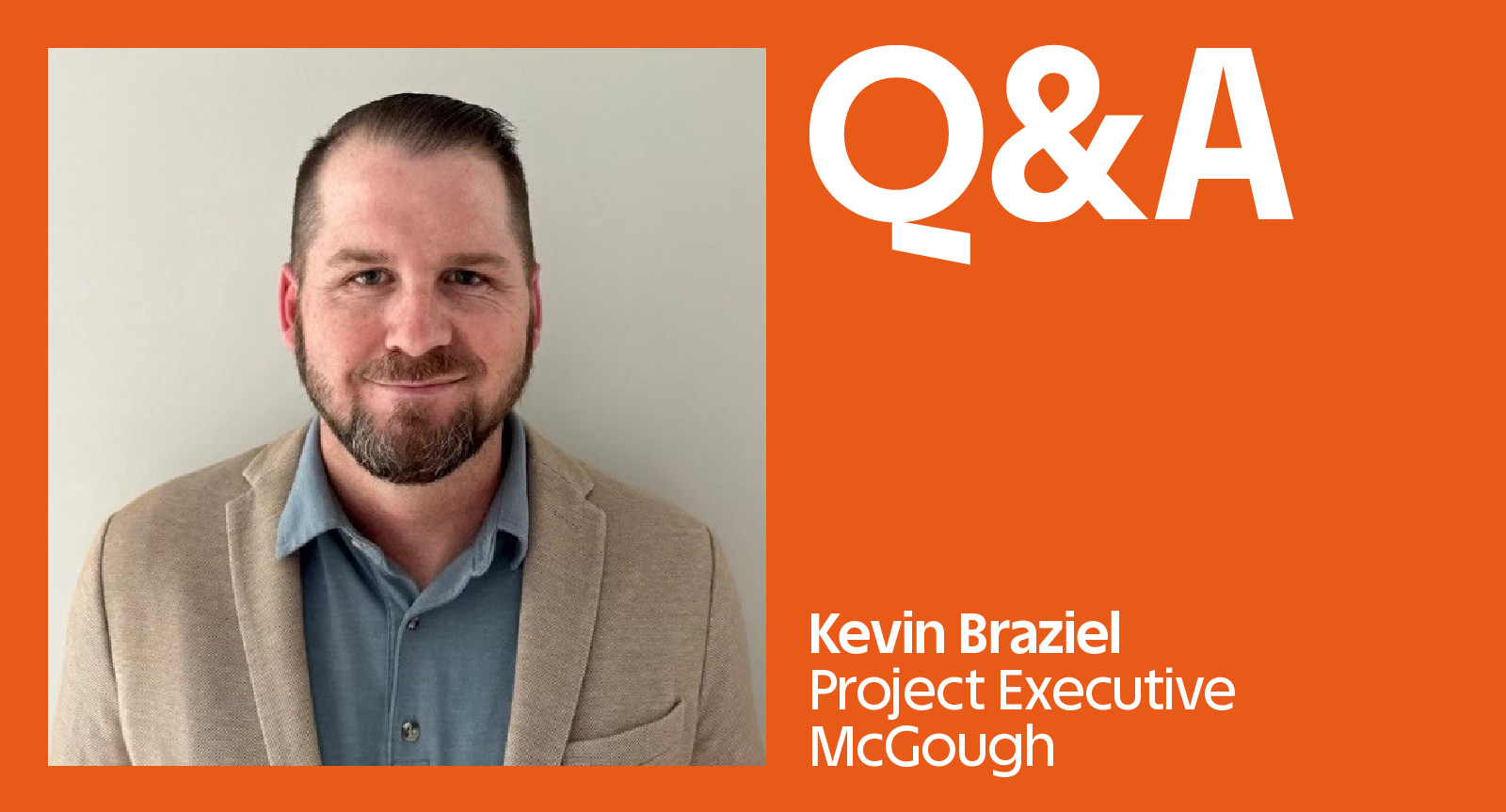
Background: Progressed from Project Manager to Project Executive across various general contractors, with experience in the pharmaceutical and life sciences sectors.
What was your familiarity with lean previously?
Quite a bit. I worked on a large project where the Last Planner System (LPS) was required as the primary planning tool by a previous general contractor.
What do you feel like the limits of lean are?
The biggest limitation is team dynamics. If your team isn’t aligned and fully bought into lean, it just becomes a set of pretty pictures on a wall—more of a conversation piece than a practical tool.
At a previous GC, there was a mandate to practice lean principles, but it wasn’t clearly defined. It turned into a check-the-box exercise. A dedicated group was tasked with implementing lean, but they ended up going through the motions without meaningful outcomes.
No one was learning anything, which completely devalued the process. If we’d continued on that path, all 27 team members would have dismissed lean entirely in future projects. If your team doesn’t understand or believe in its importance, don’t even bother.
How have you experienced Midion going beyond lean construction?
Midion has elevated the approach by emphasizing team building—through workshops, individual and team coaching, communication strategies, and events like LEGO Serious Play.
I can’t stress enough how crucial team dynamics are. I’ve told my current team they need to be all in—or not in at all. Bringing in Midion as a consultant focused on team cohesion helped to ensure everyone understands the process and commits fully.
What advice do you have for other leaders looking to grow beyond lean?
If your team isn’t functioning as a cohesive unit, don’t even think about implementing lean. Focus on building the team first!
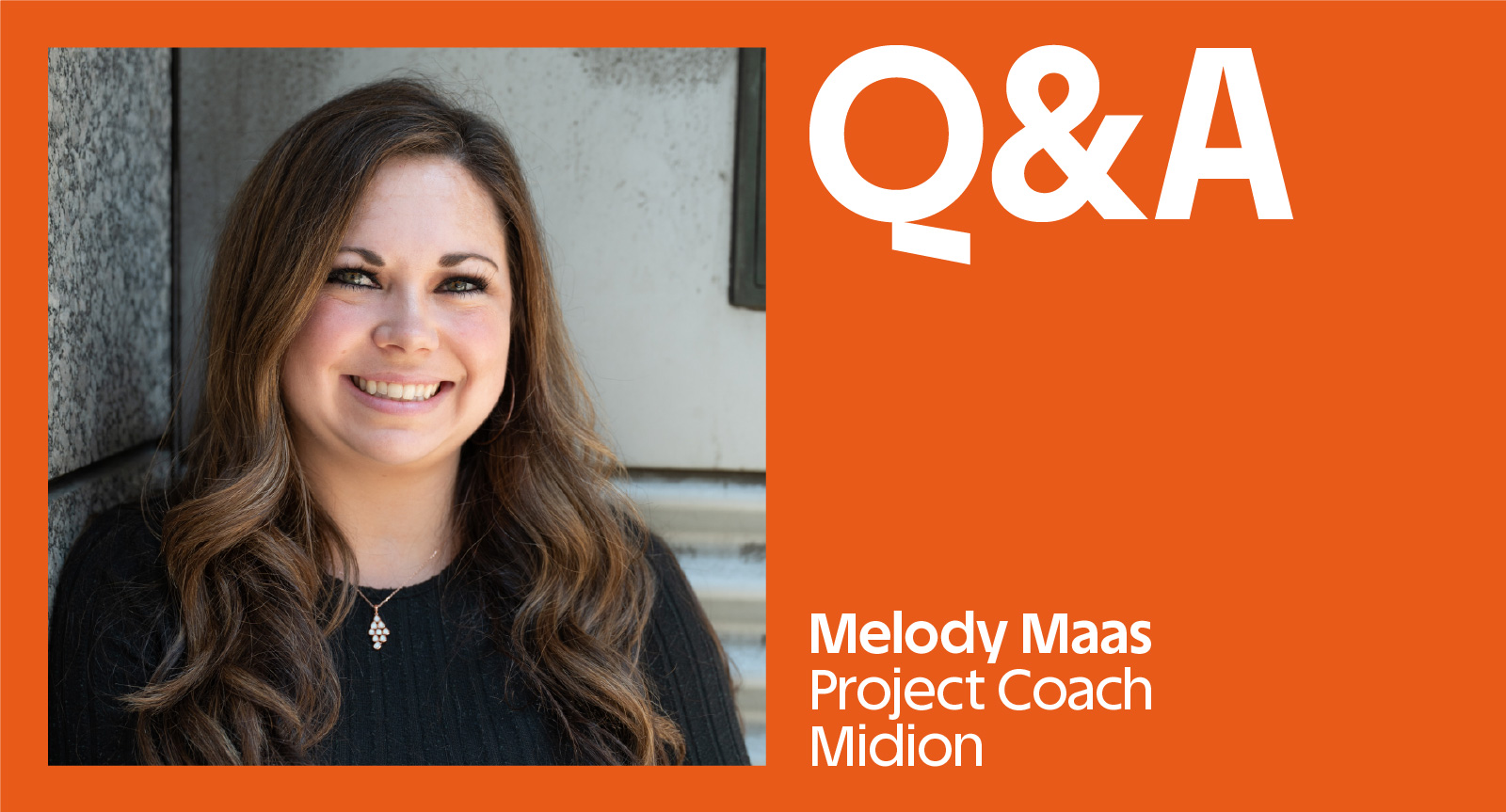
Background: Started out as a chemical engineer, then moved into construction. Progressed from Project Engineer to Assistant Project Manager for a global general contractor on semiconductor projects.
What was your familiarity with lean prior to Midion?
When I first got into construction, the general contractor I worked for was already using lean practices like the Last Planner System—things like Weekly Work Plans and Pull Planning were just part of how we operated.
Before that, I studied chemical engineering, which is also known as process engineering. We were always looking for ways to simplify systems and reduce waste in our experiments and production, so in a way, I was already thinking lean before I even knew what it was in a construction context.
What do you feel like the limits of lean are?
Lean is effective when everyone’s on board and trained well. But even with the perfect process, the project can still fall apart if the team’s not aligned.
Lean focuses on streamlining production and cutting out waste, but it doesn’t always account for the human side of construction—the personalities, the communication styles, the constant changes. If the team isn’t all moving in the same direction, lean won’t save the project.
How have you experienced Midion going beyond lean construction?
What really makes a difference at Midion is the focus on people. The coaching, workshops, and communication tools we use have a huge impact—not just on the project, but on people’s careers.
One of the first things we do with a team is figure out everyone’s Enneagram type. It helps people understand themselves and each other—how they show up, what their strengths are, where they might need support. Then we help individuals recognize the strengths and weaknesses of their type to identify where to put their efforts; whether that be being the go-to person for a certain task, growing confidence in weaker areas, or being comfortable to ask someone for help that has a clear strength in an area.
When leadership is part of that process (which is key), it sets the tone for the whole team. That’s when lean tools like the Last Planner System actually stick—because the team’s communicating openly and working as one unit.
If we’d skipped all of that and just jumped into LPS, there’s no way we’d have open communication while planning work. You have to build the trust and connection first.
What advice do you have for other leaders looking to grow beyond lean?
Start with relationships. Construction is full of tough personalities and high pressure situations, so your project team needs to be a place where people feel safe and supported.
Sometimes that shift happens naturally when a few peer leaders step up, but it works significantly better when leadership is intentional about it from the start.
And if you’re someone who sees the value in going beyond lean but isn’t sure where to start—Midion’s here for that. We’re all about helping teams work better and move the project forward by focusing on the people first.
Q&A: Melody Maas, Midion and Kevin Braziel, McGough
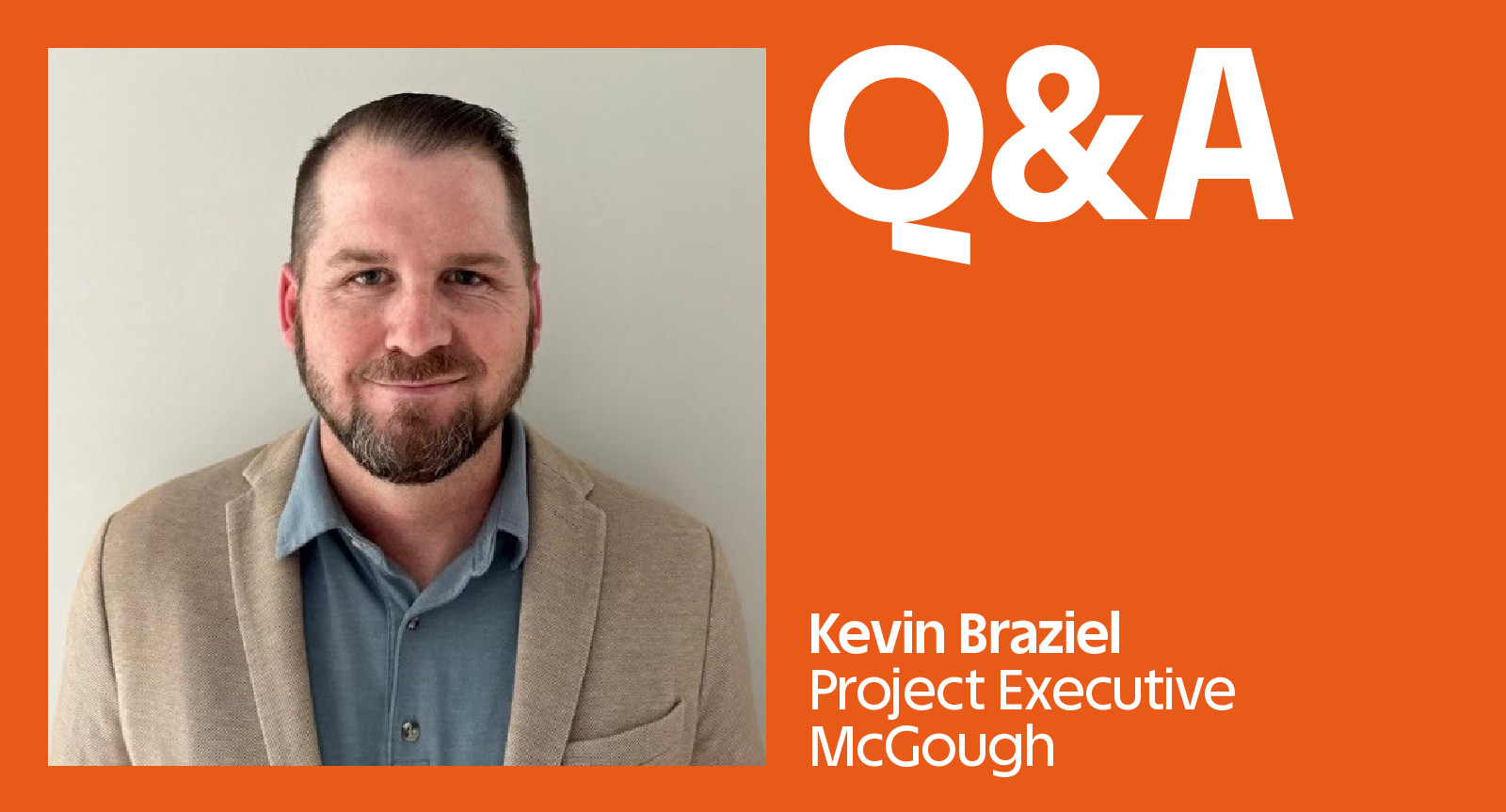
Background: Progressed from Project Manager to Project Executive across various general contractors, with experience in the pharmaceutical and life sciences sectors.
What was your familiarity with lean previously?
Quite a bit. I worked on a large project where the Last Planner System (LPS) was required as the primary planning tool by a previous general contractor.
What do you feel like the limits of lean are?
The biggest limitation is team dynamics. If your team isn’t aligned and fully bought into lean, it just becomes a set of pretty pictures on a wall—more of a conversation piece than a practical tool.
At a previous GC, there was a mandate to practice lean principles, but it wasn’t clearly defined. It turned into a check-the-box exercise. A dedicated group was tasked with implementing lean, but they ended up going through the motions without meaningful outcomes.
No one was learning anything, which completely devalued the process. If we’d continued on that path, all 27 team members would have dismissed lean entirely in future projects. If your team doesn’t understand or believe in its importance, don’t even bother.
How have you experienced Midion going beyond lean construction?
Midion has elevated the approach by emphasizing team building—through workshops, individual and team coaching, communication strategies, and events like LEGO Serious Play.
I can’t stress enough how crucial team dynamics are. I’ve told my current team they need to be all in—or not in at all. Bringing in Midion as a consultant focused on team cohesion helped to ensure everyone understands the process and commits fully.
What advice do you have for other leaders looking to grow beyond lean?
If your team isn’t functioning as a cohesive unit, don’t even think about implementing lean. Focus on building the team first!
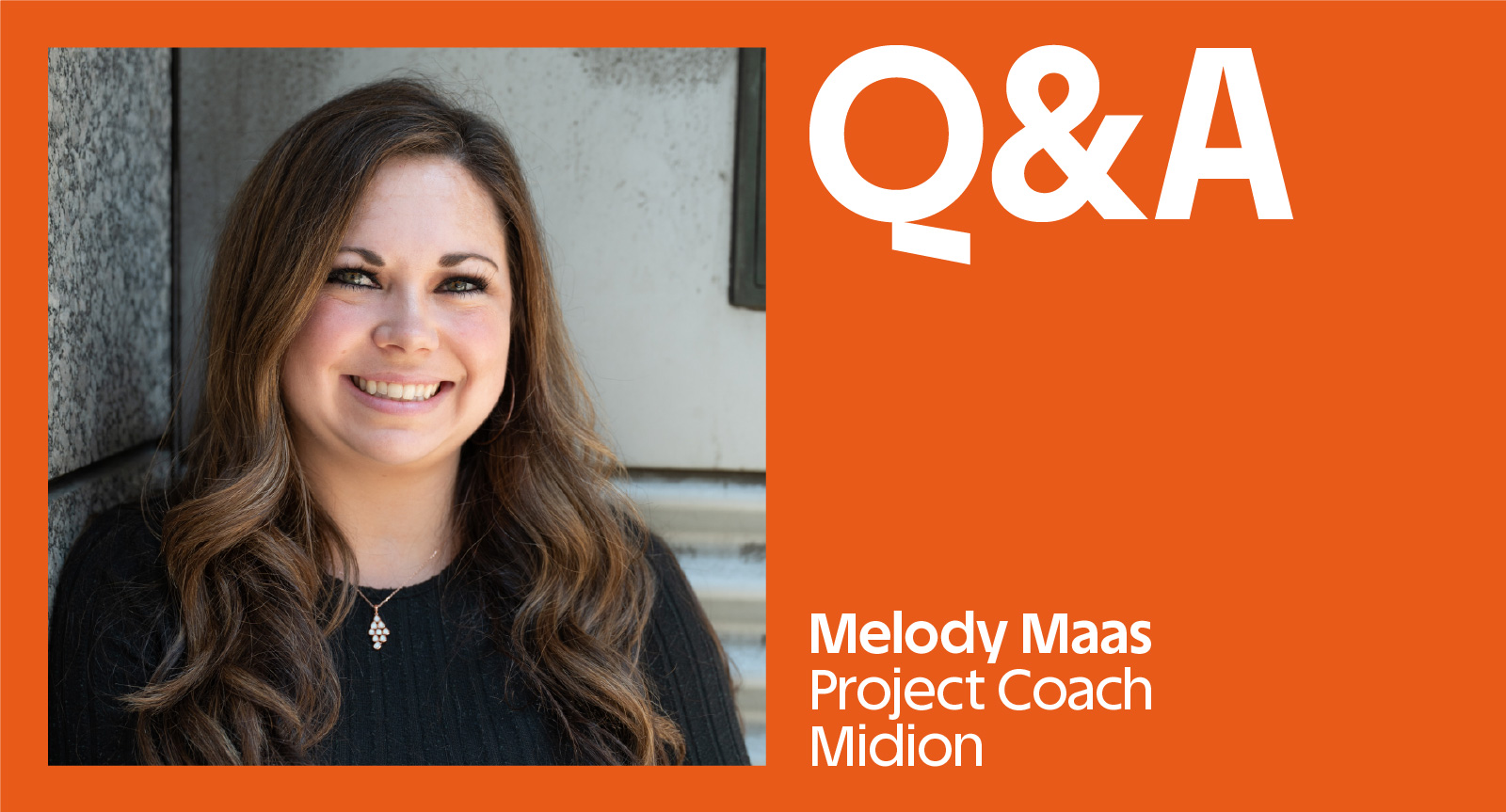
Background: Started out as a chemical engineer, then moved into construction. Progressed from Project Engineer to Assistant Project Manager for a global general contractor on semiconductor projects.
What was your familiarity with lean prior to Midion?
When I first got into construction, the general contractor I worked for was already using lean practices like the Last Planner System—things like Weekly Work Plans and Pull Planning were just part of how we operated.
Before that, I studied chemical engineering, which is also known as process engineering. We were always looking for ways to simplify systems and reduce waste in our experiments and production, so in a way, I was already thinking lean before I even knew what it was in a construction context.
What do you feel like the limits of lean are?
Lean is effective when everyone’s on board and trained well. But even with the perfect process, the project can still fall apart if the team’s not aligned.
Lean focuses on streamlining production and cutting out waste, but it doesn’t always account for the human side of construction—the personalities, the communication styles, the constant changes. If the team isn’t all moving in the same direction, lean won’t save the project.
How have you experienced Midion going beyond lean construction?
What really makes a difference at Midion is the focus on people. The coaching, workshops, and communication tools we use have a huge impact—not just on the project, but on people’s careers.
One of the first things we do with a team is figure out everyone’s Enneagram type. It helps people understand themselves and each other—how they show up, what their strengths are, where they might need support. Then we help individuals recognize the strengths and weaknesses of their type to identify where to put their efforts; whether that be being the go-to person for a certain task, growing confidence in weaker areas, or being comfortable to ask someone for help that has a clear strength in an area.
When leadership is part of that process (which is key), it sets the tone for the whole team. That’s when lean tools like the Last Planner System actually stick—because the team’s communicating openly and working as one unit.
If we’d skipped all of that and just jumped into LPS, there’s no way we’d have open communication while planning work. You have to build the trust and connection first.
What advice do you have for other leaders looking to grow beyond lean?
Start with relationships. Construction is full of tough personalities and high pressure situations, so your project team needs to be a place where people feel safe and supported.
Sometimes that shift happens naturally when a few peer leaders step up, but it works significantly better when leadership is intentional about it from the start.
And if you’re someone who sees the value in going beyond lean but isn’t sure where to start—Midion’s here for that. We’re all about helping teams work better and move the project forward by focusing on the people first.
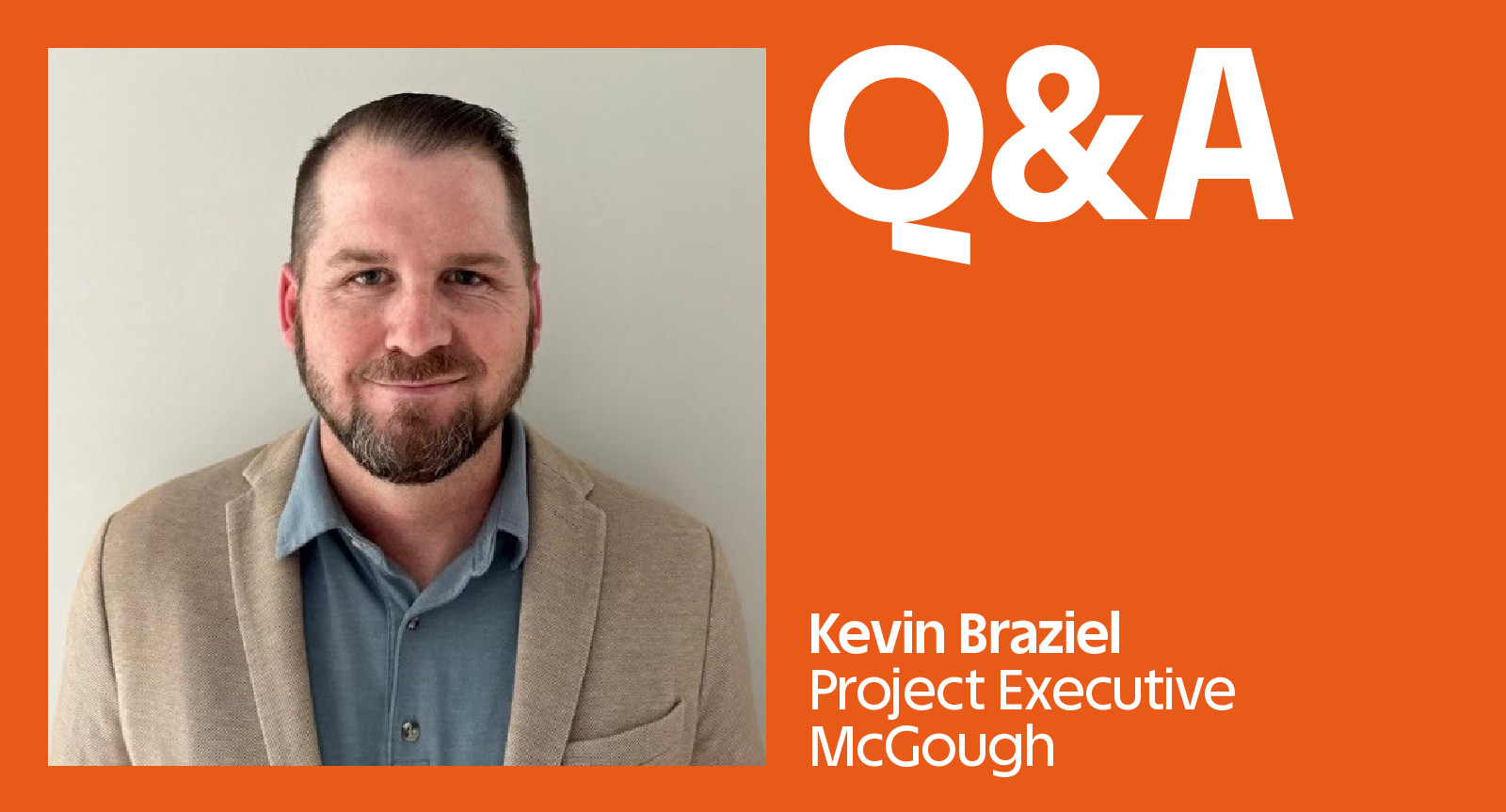
Background: Progressed from Project Manager to Project Executive across various general contractors, with experience in the pharmaceutical and life sciences sectors.
What was your familiarity with lean previously?
Quite a bit. I worked on a large project where the Last Planner System (LPS) was required as the primary planning tool by a previous general contractor.
What do you feel like the limits of lean are?
The biggest limitation is team dynamics. If your team isn’t aligned and fully bought into lean, it just becomes a set of pretty pictures on a wall—more of a conversation piece than a practical tool.
At a previous GC, there was a mandate to practice lean principles, but it wasn’t clearly defined. It turned into a check-the-box exercise. A dedicated group was tasked with implementing lean, but they ended up going through the motions without meaningful outcomes.
No one was learning anything, which completely devalued the process. If we’d continued on that path, all 27 team members would have dismissed lean entirely in future projects. If your team doesn’t understand or believe in its importance, don’t even bother.
How have you experienced Midion going beyond lean construction?
Midion has elevated the approach by emphasizing team building—through workshops, individual and team coaching, communication strategies, and events like LEGO Serious Play.
I can’t stress enough how crucial team dynamics are. I’ve told my current team they need to be all in—or not in at all. Bringing in Midion as a consultant focused on team cohesion helped to ensure everyone understands the process and commits fully.
What advice do you have for other leaders looking to grow beyond lean?
If your team isn’t functioning as a cohesive unit, don’t even think about implementing lean. Focus on building the team first!
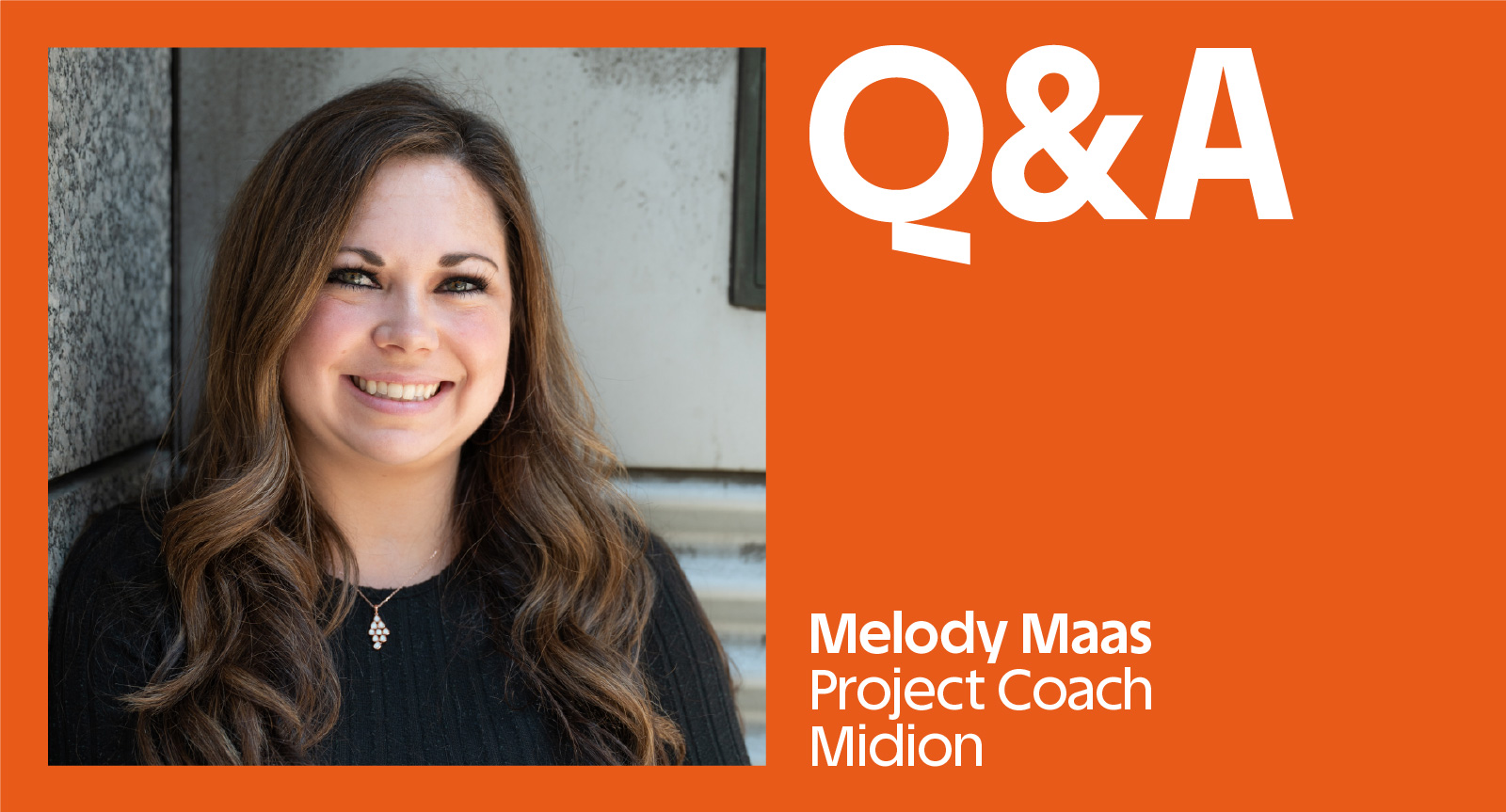
Background: Started out as a chemical engineer, then moved into construction. Progressed from Project Engineer to Assistant Project Manager for a global general contractor on semiconductor projects.
What was your familiarity with lean prior to Midion?
When I first got into construction, the general contractor I worked for was already using lean practices like the Last Planner System—things like Weekly Work Plans and Pull Planning were just part of how we operated.
Before that, I studied chemical engineering, which is also known as process engineering. We were always looking for ways to simplify systems and reduce waste in our experiments and production, so in a way, I was already thinking lean before I even knew what it was in a construction context.
What do you feel like the limits of lean are?
Lean is effective when everyone’s on board and trained well. But even with the perfect process, the project can still fall apart if the team’s not aligned.
Lean focuses on streamlining production and cutting out waste, but it doesn’t always account for the human side of construction—the personalities, the communication styles, the constant changes. If the team isn’t all moving in the same direction, lean won’t save the project.
How have you experienced Midion going beyond lean construction?
What really makes a difference at Midion is the focus on people. The coaching, workshops, and communication tools we use have a huge impact—not just on the project, but on people’s careers.
One of the first things we do with a team is figure out everyone’s Enneagram type. It helps people understand themselves and each other—how they show up, what their strengths are, where they might need support. Then we help individuals recognize the strengths and weaknesses of their type to identify where to put their efforts; whether that be being the go-to person for a certain task, growing confidence in weaker areas, or being comfortable to ask someone for help that has a clear strength in an area.
When leadership is part of that process (which is key), it sets the tone for the whole team. That’s when lean tools like the Last Planner System actually stick—because the team’s communicating openly and working as one unit.
If we’d skipped all of that and just jumped into LPS, there’s no way we’d have open communication while planning work. You have to build the trust and connection first.
What advice do you have for other leaders looking to grow beyond lean?
Start with relationships. Construction is full of tough personalities and high pressure situations, so your project team needs to be a place where people feel safe and supported.
Sometimes that shift happens naturally when a few peer leaders step up, but it works significantly better when leadership is intentional about it from the start.
And if you’re someone who sees the value in going beyond lean but isn’t sure where to start—Midion’s here for that. We’re all about helping teams work better and move the project forward by focusing on the people first.
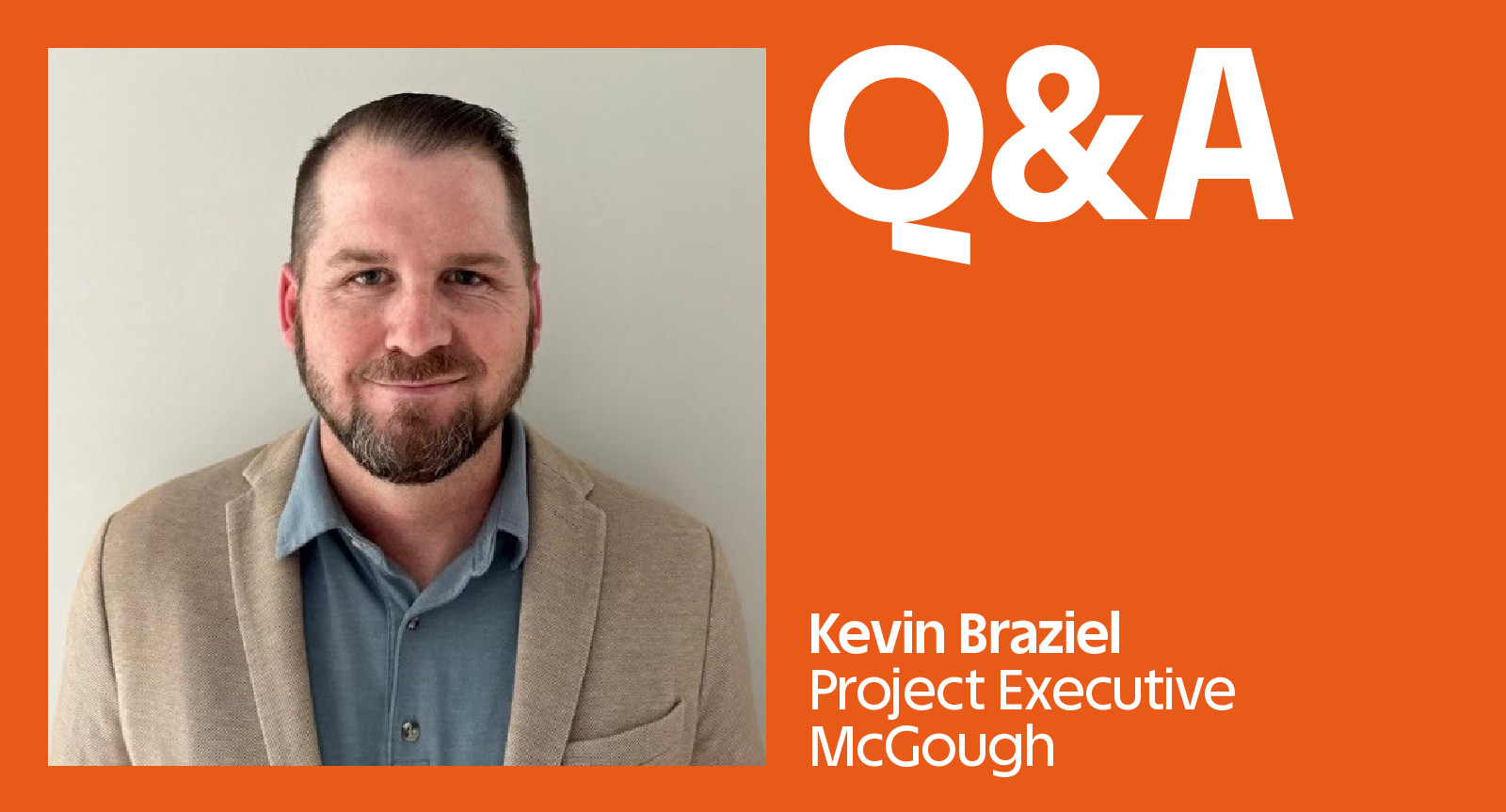
Background: Progressed from Project Manager to Project Executive across various general contractors, with experience in the pharmaceutical and life sciences sectors.
What was your familiarity with lean previously?
Quite a bit. I worked on a large project where the Last Planner System (LPS) was required as the primary planning tool by a previous general contractor.
What do you feel like the limits of lean are?
The biggest limitation is team dynamics. If your team isn’t aligned and fully bought into lean, it just becomes a set of pretty pictures on a wall—more of a conversation piece than a practical tool.
At a previous GC, there was a mandate to practice lean principles, but it wasn’t clearly defined. It turned into a check-the-box exercise. A dedicated group was tasked with implementing lean, but they ended up going through the motions without meaningful outcomes.
No one was learning anything, which completely devalued the process. If we’d continued on that path, all 27 team members would have dismissed lean entirely in future projects. If your team doesn’t understand or believe in its importance, don’t even bother.
How have you experienced Midion going beyond lean construction?
Midion has elevated the approach by emphasizing team building—through workshops, individual and team coaching, communication strategies, and events like LEGO Serious Play.
I can’t stress enough how crucial team dynamics are. I’ve told my current team they need to be all in—or not in at all. Bringing in Midion as a consultant focused on team cohesion helped to ensure everyone understands the process and commits fully.
What advice do you have for other leaders looking to grow beyond lean?
If your team isn’t functioning as a cohesive unit, don’t even think about implementing lean. Focus on building the team first!
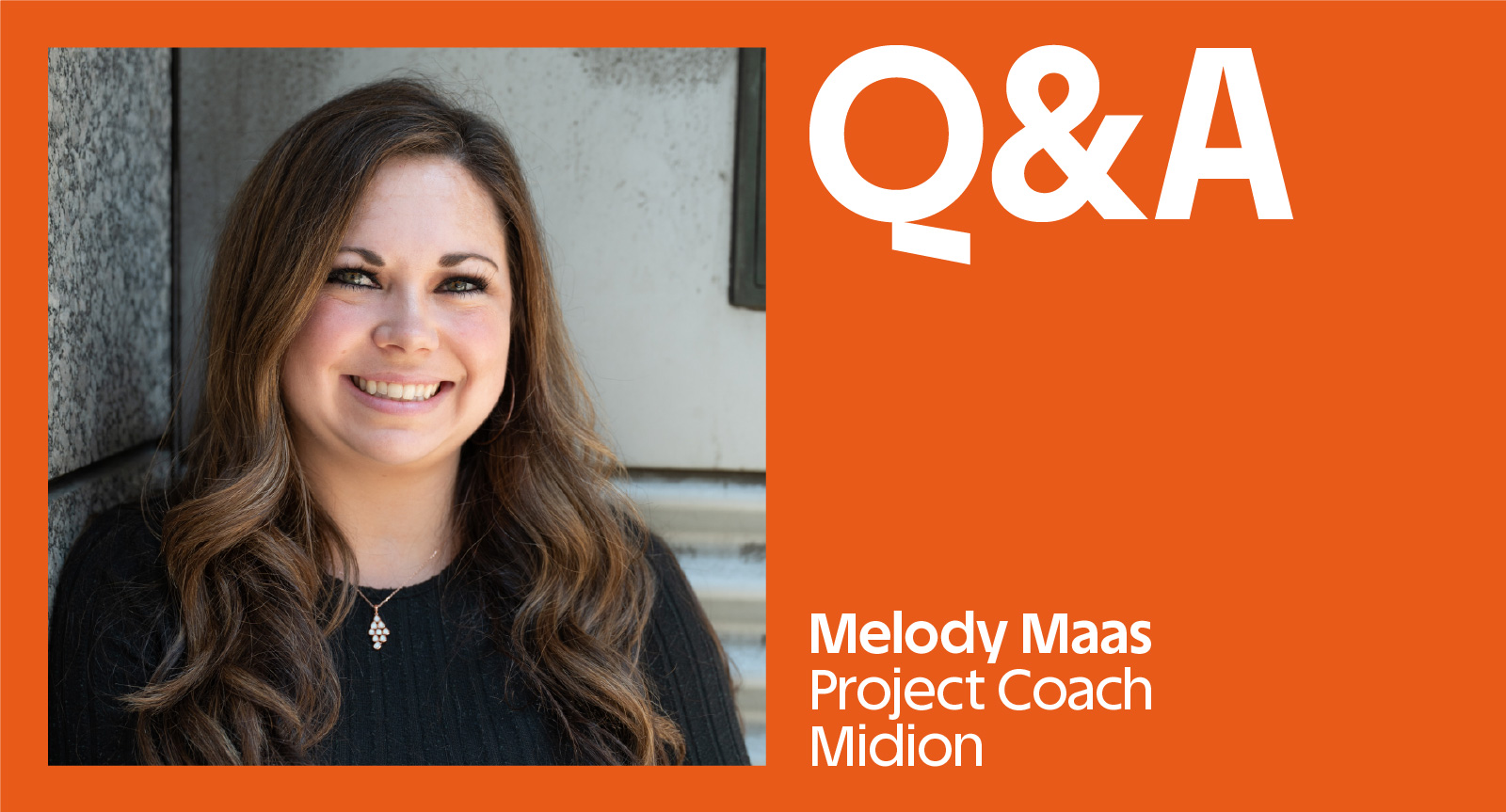
Background: Started out as a chemical engineer, then moved into construction. Progressed from Project Engineer to Assistant Project Manager for a global general contractor on semiconductor projects.
What was your familiarity with lean prior to Midion?
When I first got into construction, the general contractor I worked for was already using lean practices like the Last Planner System—things like Weekly Work Plans and Pull Planning were just part of how we operated.
Before that, I studied chemical engineering, which is also known as process engineering. We were always looking for ways to simplify systems and reduce waste in our experiments and production, so in a way, I was already thinking lean before I even knew what it was in a construction context.
What do you feel like the limits of lean are?
Lean is effective when everyone’s on board and trained well. But even with the perfect process, the project can still fall apart if the team’s not aligned.
Lean focuses on streamlining production and cutting out waste, but it doesn’t always account for the human side of construction—the personalities, the communication styles, the constant changes. If the team isn’t all moving in the same direction, lean won’t save the project.
How have you experienced Midion going beyond lean construction?
What really makes a difference at Midion is the focus on people. The coaching, workshops, and communication tools we use have a huge impact—not just on the project, but on people’s careers.
One of the first things we do with a team is figure out everyone’s Enneagram type. It helps people understand themselves and each other—how they show up, what their strengths are, where they might need support. Then we help individuals recognize the strengths and weaknesses of their type to identify where to put their efforts; whether that be being the go-to person for a certain task, growing confidence in weaker areas, or being comfortable to ask someone for help that has a clear strength in an area.
When leadership is part of that process (which is key), it sets the tone for the whole team. That’s when lean tools like the Last Planner System actually stick—because the team’s communicating openly and working as one unit.
If we’d skipped all of that and just jumped into LPS, there’s no way we’d have open communication while planning work. You have to build the trust and connection first.
What advice do you have for other leaders looking to grow beyond lean?
Start with relationships. Construction is full of tough personalities and high pressure situations, so your project team needs to be a place where people feel safe and supported.
Sometimes that shift happens naturally when a few peer leaders step up, but it works significantly better when leadership is intentional about it from the start.
And if you’re someone who sees the value in going beyond lean but isn’t sure where to start—Midion’s here for that. We’re all about helping teams work better and move the project forward by focusing on the people first.
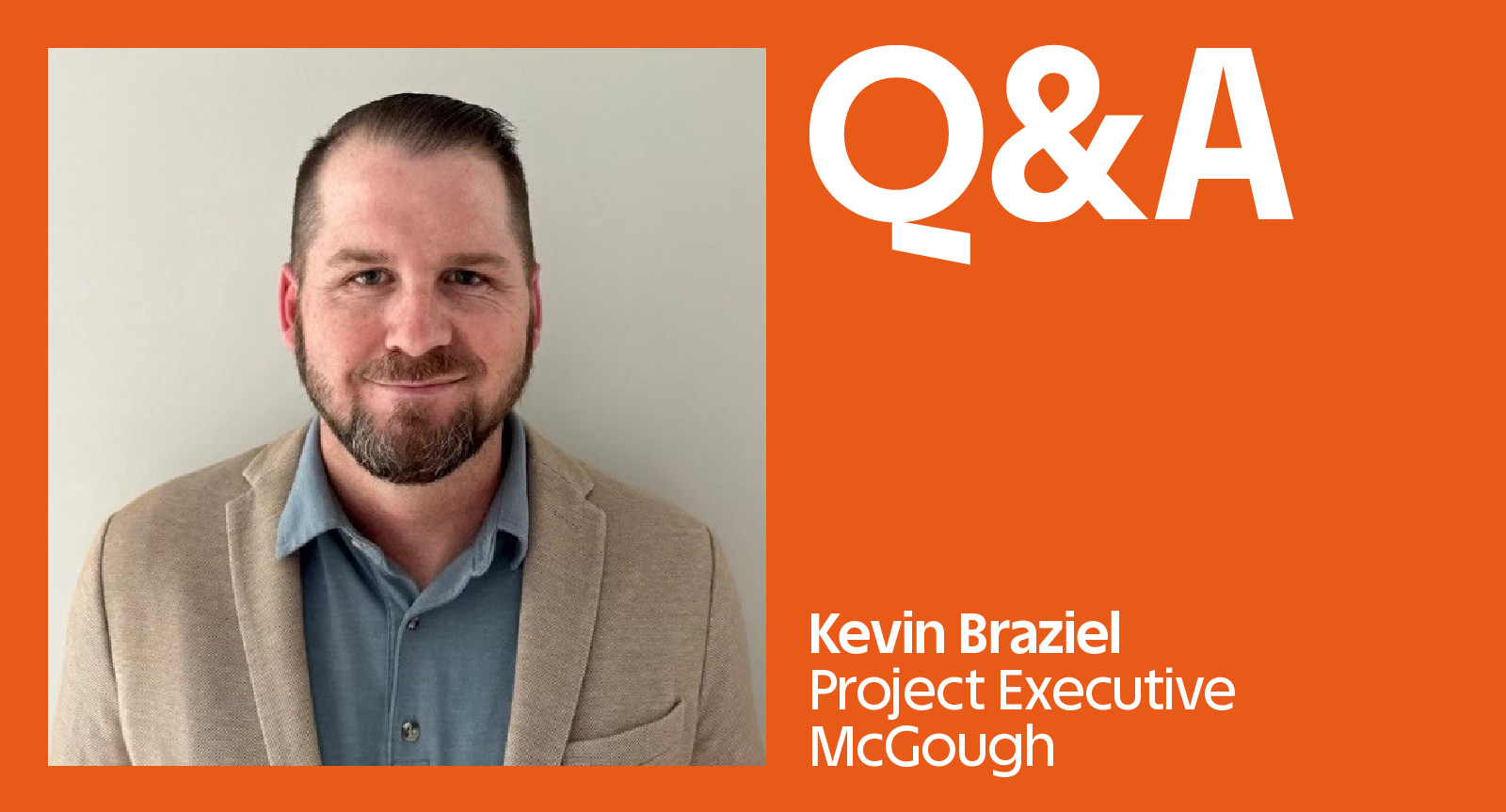
Background: Progressed from Project Manager to Project Executive across various general contractors, with experience in the pharmaceutical and life sciences sectors.
What was your familiarity with lean previously?
Quite a bit. I worked on a large project where the Last Planner System (LPS) was required as the primary planning tool by a previous general contractor.
What do you feel like the limits of lean are?
The biggest limitation is team dynamics. If your team isn’t aligned and fully bought into lean, it just becomes a set of pretty pictures on a wall—more of a conversation piece than a practical tool.
At a previous GC, there was a mandate to practice lean principles, but it wasn’t clearly defined. It turned into a check-the-box exercise. A dedicated group was tasked with implementing lean, but they ended up going through the motions without meaningful outcomes.
No one was learning anything, which completely devalued the process. If we’d continued on that path, all 27 team members would have dismissed lean entirely in future projects. If your team doesn’t understand or believe in its importance, don’t even bother.
How have you experienced Midion going beyond lean construction?
Midion has elevated the approach by emphasizing team building—through workshops, individual and team coaching, communication strategies, and events like LEGO Serious Play.
I can’t stress enough how crucial team dynamics are. I’ve told my current team they need to be all in—or not in at all. Bringing in Midion as a consultant focused on team cohesion helped to ensure everyone understands the process and commits fully.
What advice do you have for other leaders looking to grow beyond lean?
If your team isn’t functioning as a cohesive unit, don’t even think about implementing lean. Focus on building the team first!
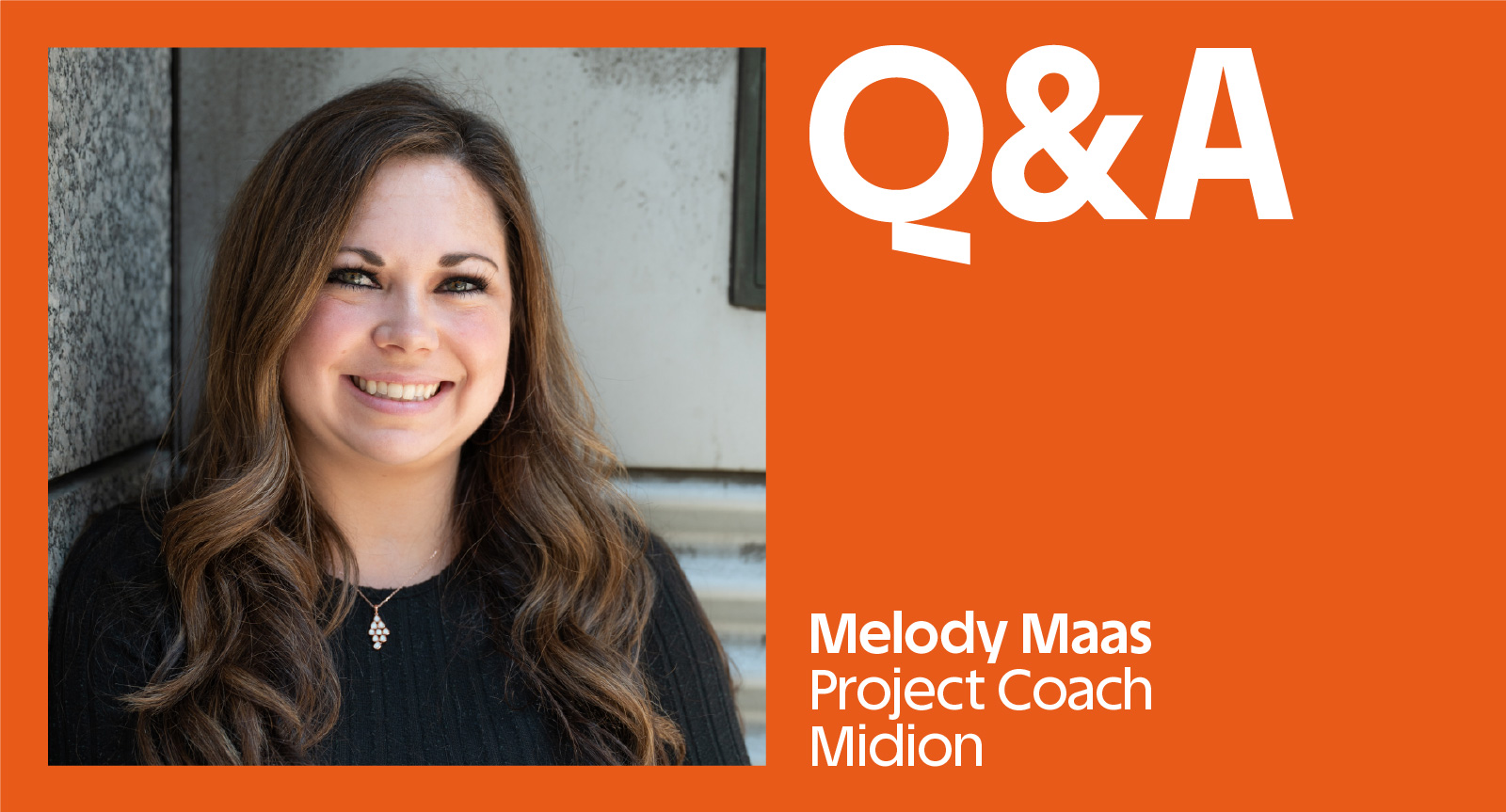
Background: Started out as a chemical engineer, then moved into construction. Progressed from Project Engineer to Assistant Project Manager for a global general contractor on semiconductor projects.
What was your familiarity with lean prior to Midion?
When I first got into construction, the general contractor I worked for was already using lean practices like the Last Planner System—things like Weekly Work Plans and Pull Planning were just part of how we operated.
Before that, I studied chemical engineering, which is also known as process engineering. We were always looking for ways to simplify systems and reduce waste in our experiments and production, so in a way, I was already thinking lean before I even knew what it was in a construction context.
What do you feel like the limits of lean are?
Lean is effective when everyone’s on board and trained well. But even with the perfect process, the project can still fall apart if the team’s not aligned.
Lean focuses on streamlining production and cutting out waste, but it doesn’t always account for the human side of construction—the personalities, the communication styles, the constant changes. If the team isn’t all moving in the same direction, lean won’t save the project.
How have you experienced Midion going beyond lean construction?
What really makes a difference at Midion is the focus on people. The coaching, workshops, and communication tools we use have a huge impact—not just on the project, but on people’s careers.
One of the first things we do with a team is figure out everyone’s Enneagram type. It helps people understand themselves and each other—how they show up, what their strengths are, where they might need support. Then we help individuals recognize the strengths and weaknesses of their type to identify where to put their efforts; whether that be being the go-to person for a certain task, growing confidence in weaker areas, or being comfortable to ask someone for help that has a clear strength in an area.
When leadership is part of that process (which is key), it sets the tone for the whole team. That’s when lean tools like the Last Planner System actually stick—because the team’s communicating openly and working as one unit.
If we’d skipped all of that and just jumped into LPS, there’s no way we’d have open communication while planning work. You have to build the trust and connection first.
What advice do you have for other leaders looking to grow beyond lean?
Start with relationships. Construction is full of tough personalities and high pressure situations, so your project team needs to be a place where people feel safe and supported.
Sometimes that shift happens naturally when a few peer leaders step up, but it works significantly better when leadership is intentional about it from the start.
And if you’re someone who sees the value in going beyond lean but isn’t sure where to start—Midion’s here for that. We’re all about helping teams work better and move the project forward by focusing on the people first.