Why Lean Construction Can Leave You Stuck
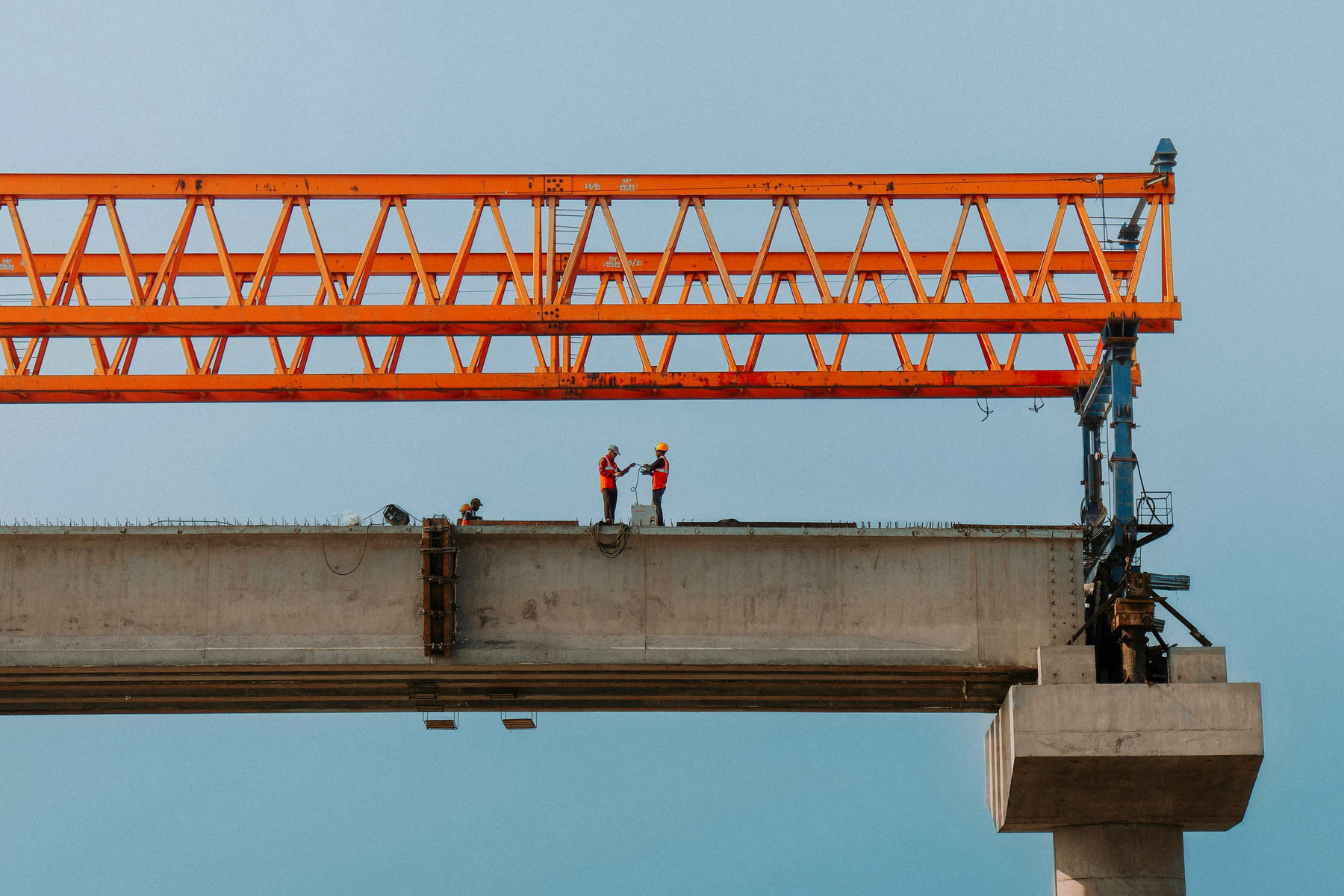
Why Lean Construction Can Leave You Stuck
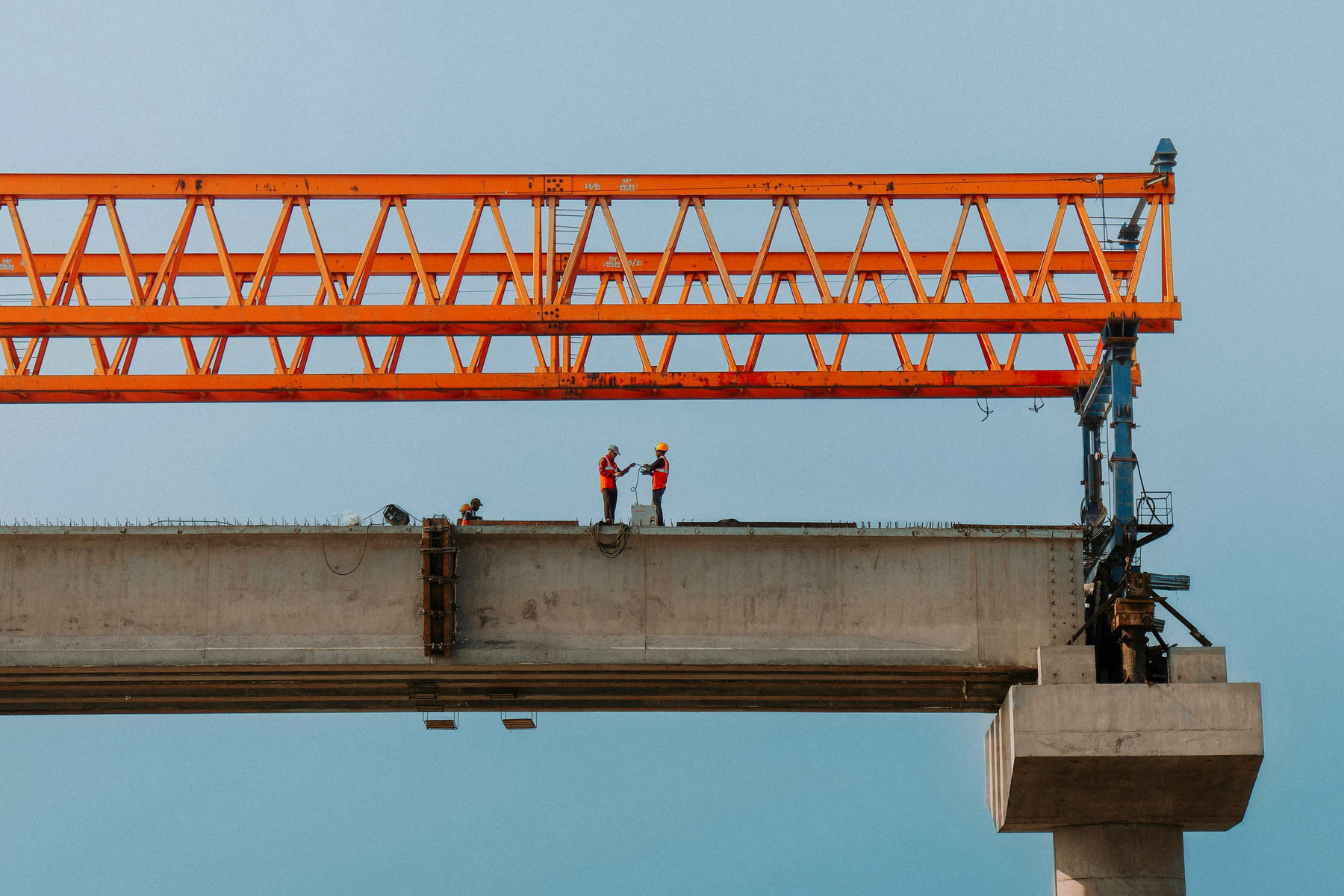
Lean construction has long been praised for boosting efficiency, cutting waste, and streamlining project delivery. And yes, it works…to a point. But if you’re managing complex construction projects with multiple stakeholders, shifting goals, and high stakes, Lean alone simply can’t address the deeper issues that derail progress.
Many teams still treat Lean as the ultimate solution. It’s not, and it might just leave you stuck.
Lean’s Limitations in Modern Construction Project Management
What is lean construction?
Lean construction is built around production-based thinking: reduce waste, improve flow, optimize processes. But today’s large-scale construction projects aren’t factories. They’re ecosystems of interdependent teams, layered decision-making, and evolving priorities.
Lean construction typically overlooks:
- Cross-organizational collaboration challenges
- Misaligned incentives between owners, designers, and contractors
- Ambiguity in leadership, decision-making, and accountability
- Communication breakdowns in fast-moving environments
- Gaps in the skills of project participants
Lean methods assume a baseline of clarity and cooperation that rarely exists at the scale and complexity of today’s projects.
What Happens When Lean Isn’t Enough?
You’ve invested in Lean construction tools. Your team is holding planning sessions. Your schedules and checklists are in place. But the project still feels sluggish. Unfortunately, ensuring on-time, on-budget delivery while managing human coordination, uncertainty, and evolving challenges is difficult. That’s where relying solely on lean construction can fall short.
Here’s what we see when Lean falls short:
- Execution suffers despite thorough preplanning
- The project team hits delays caused by unclear decisions
- Meeting fatigue grows, but real alignment is missing
- Subcontractors follow the process, but outcomes don’t improve
Lean frameworks can make teams feel productive while critical misalignments go unresolved. This problem showed up in a recent Cleveland Clinic project, where Lean tools weren’t enough to solve the collaboration and communication challenges. The team needed something more. With three critical new projects on the horizon, the team knew they'd need a new approach to avoid the delays, cost overruns, and frustrations that were typical in the past. The solution required support at two levels.
First, the team implemented a new delivery model based on Integrated Project Delivery principles. Then, for each of the three sub-projects simultaneously being executed, a Senior Management Team, a Core Team, and a Project Execution Team were established for each. In the field, a robust Last Planner System was implemented for each project, including pull planning, weekly Work Planning, Make-Ready Planning, Daily Huddles, and tracking of PPC and variances.
As a result, all three builds were completed on time and within budget.
Download our Zero Punch List White Paper to learn more:
How the Midion Method Goes Beyond Lean
What is the Midion Method?
Over the last 25 years, the team at Midion has partnered on some of the most challenging projects and engaged in the most significant innovation conversations in construction and design. From these experiences, Midion has created a better way to work that inspires hope and promises a brighter future for the industry. It’s called the Midion Method.
The Midion Method was built to handle what Lean construction cannot: the people side of complex project management. It’s not about replacing Lean—it’s about expanding beyond it to make it work.
What makes the Midion Method different?
- Clarifies ownership. Define who owns what across companies and teams.
- Aligns stakeholders. Get decision-makers, builders, and planners on the same page.
- Builds durable communication rhythms. Move from vague meetings to structured, actionable dialogues.
- Adapts to complexity. Support systems evolve as the project does, without rigidity.
- Develops skills needed for team members to thrive together.
This isn’t theory. The Midion Method has been tested and proven on complex builds with multiple firms, tight timelines, and high stakes.
Discover the Midion Method:
Don’t Let Lean Construction Limit Your Project’s Potential
Lean is a great starting point. But it wasn’t designed to handle the real-world chaos, complexity, and communication needs of modern construction project management. If your project matters, and most do, don’t leave success to a toolset that stops short. Discover the Midion Method and equip your team with what Lean left out.
Let’s Talk About Your Project:
Why Lean Construction Can Leave You Stuck
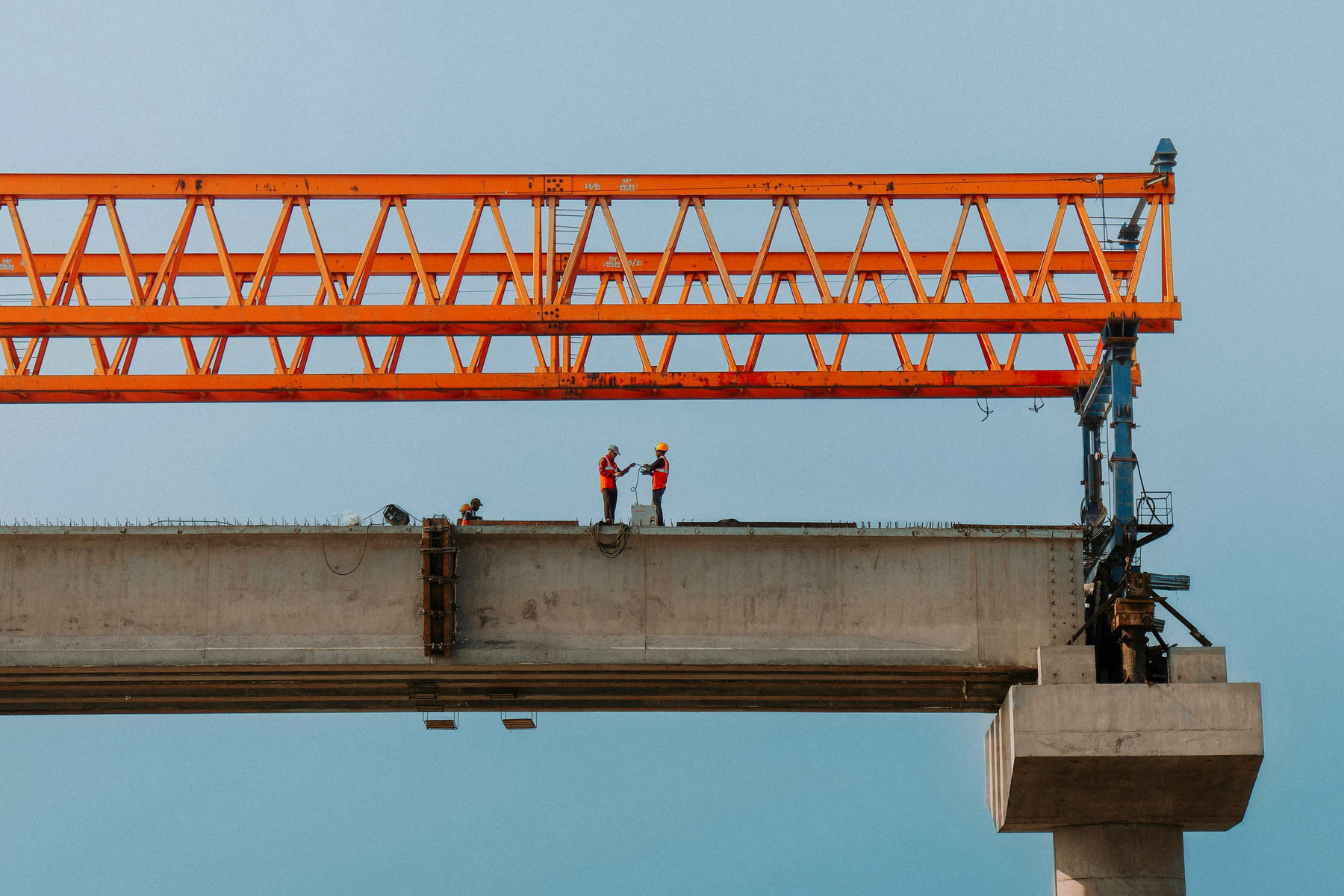
Lean construction has long been praised for boosting efficiency, cutting waste, and streamlining project delivery. And yes, it works…to a point. But if you’re managing complex construction projects with multiple stakeholders, shifting goals, and high stakes, Lean alone simply can’t address the deeper issues that derail progress.
Many teams still treat Lean as the ultimate solution. It’s not, and it might just leave you stuck.
Lean’s Limitations in Modern Construction Project Management
What is lean construction?
Lean construction is built around production-based thinking: reduce waste, improve flow, optimize processes. But today’s large-scale construction projects aren’t factories. They’re ecosystems of interdependent teams, layered decision-making, and evolving priorities.
Lean construction typically overlooks:
- Cross-organizational collaboration challenges
- Misaligned incentives between owners, designers, and contractors
- Ambiguity in leadership, decision-making, and accountability
- Communication breakdowns in fast-moving environments
- Gaps in the skills of project participants
Lean methods assume a baseline of clarity and cooperation that rarely exists at the scale and complexity of today’s projects.
What Happens When Lean Isn’t Enough?
You’ve invested in Lean construction tools. Your team is holding planning sessions. Your schedules and checklists are in place. But the project still feels sluggish. Unfortunately, ensuring on-time, on-budget delivery while managing human coordination, uncertainty, and evolving challenges is difficult. That’s where relying solely on lean construction can fall short.
Here’s what we see when Lean falls short:
- Execution suffers despite thorough preplanning
- The project team hits delays caused by unclear decisions
- Meeting fatigue grows, but real alignment is missing
- Subcontractors follow the process, but outcomes don’t improve
Lean frameworks can make teams feel productive while critical misalignments go unresolved. This problem showed up in a recent Cleveland Clinic project, where Lean tools weren’t enough to solve the collaboration and communication challenges. The team needed something more. With three critical new projects on the horizon, the team knew they'd need a new approach to avoid the delays, cost overruns, and frustrations that were typical in the past. The solution required support at two levels.
First, the team implemented a new delivery model based on Integrated Project Delivery principles. Then, for each of the three sub-projects simultaneously being executed, a Senior Management Team, a Core Team, and a Project Execution Team were established for each. In the field, a robust Last Planner System was implemented for each project, including pull planning, weekly Work Planning, Make-Ready Planning, Daily Huddles, and tracking of PPC and variances.
As a result, all three builds were completed on time and within budget.
Download our Zero Punch List White Paper to learn more:
How the Midion Method Goes Beyond Lean
What is the Midion Method?
Over the last 25 years, the team at Midion has partnered on some of the most challenging projects and engaged in the most significant innovation conversations in construction and design. From these experiences, Midion has created a better way to work that inspires hope and promises a brighter future for the industry. It’s called the Midion Method.
The Midion Method was built to handle what Lean construction cannot: the people side of complex project management. It’s not about replacing Lean—it’s about expanding beyond it to make it work.
What makes the Midion Method different?
- Clarifies ownership. Define who owns what across companies and teams.
- Aligns stakeholders. Get decision-makers, builders, and planners on the same page.
- Builds durable communication rhythms. Move from vague meetings to structured, actionable dialogues.
- Adapts to complexity. Support systems evolve as the project does, without rigidity.
- Develops skills needed for team members to thrive together.
This isn’t theory. The Midion Method has been tested and proven on complex builds with multiple firms, tight timelines, and high stakes.
Discover the Midion Method:
Don’t Let Lean Construction Limit Your Project’s Potential
Lean is a great starting point. But it wasn’t designed to handle the real-world chaos, complexity, and communication needs of modern construction project management. If your project matters, and most do, don’t leave success to a toolset that stops short. Discover the Midion Method and equip your team with what Lean left out.
Let’s Talk About Your Project:
Why Lean Construction Can Leave You Stuck
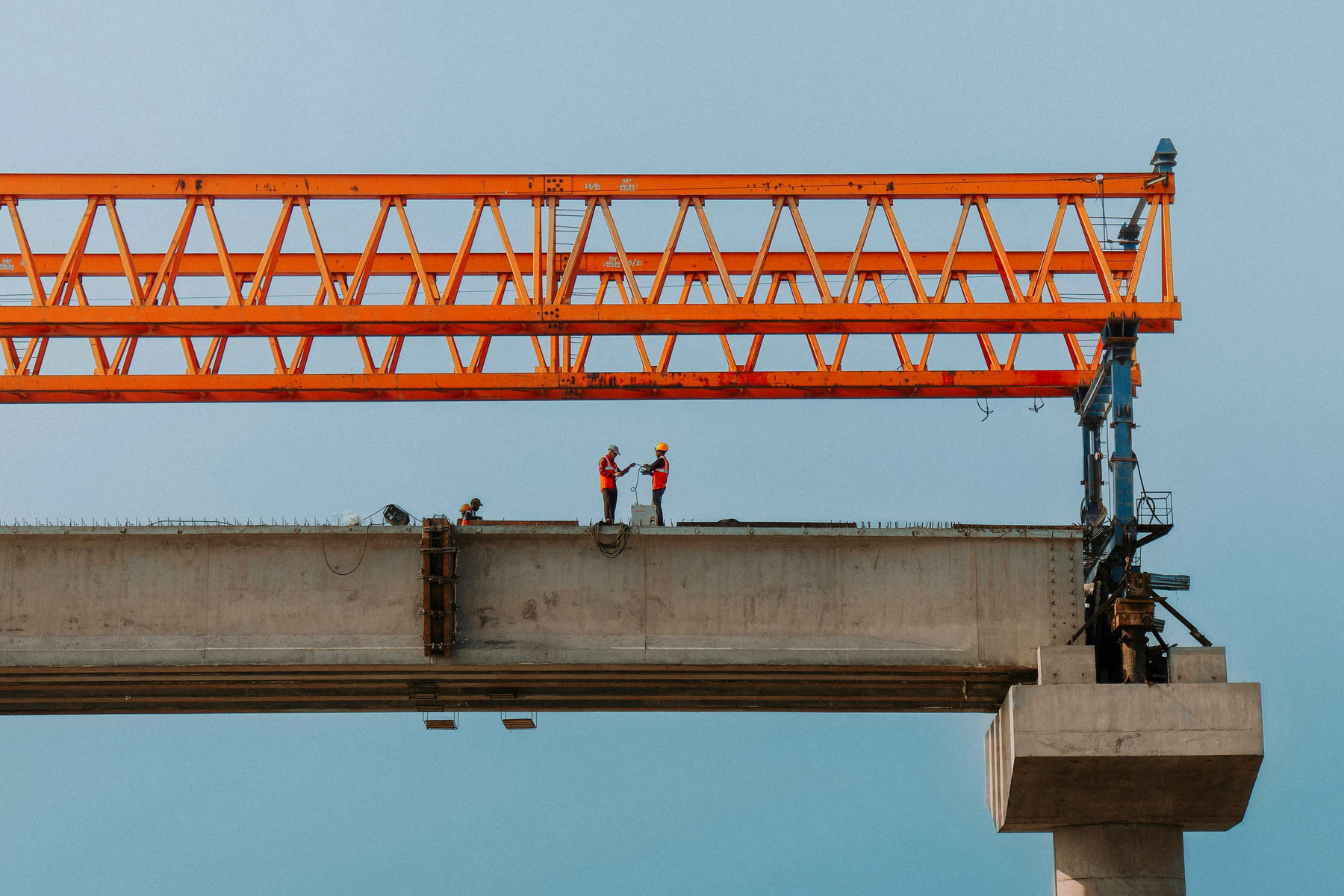
Lean construction has long been praised for boosting efficiency, cutting waste, and streamlining project delivery. And yes, it works…to a point. But if you’re managing complex construction projects with multiple stakeholders, shifting goals, and high stakes, Lean alone simply can’t address the deeper issues that derail progress.
Many teams still treat Lean as the ultimate solution. It’s not, and it might just leave you stuck.
Lean’s Limitations in Modern Construction Project Management
What is lean construction?
Lean construction is built around production-based thinking: reduce waste, improve flow, optimize processes. But today’s large-scale construction projects aren’t factories. They’re ecosystems of interdependent teams, layered decision-making, and evolving priorities.
Lean construction typically overlooks:
- Cross-organizational collaboration challenges
- Misaligned incentives between owners, designers, and contractors
- Ambiguity in leadership, decision-making, and accountability
- Communication breakdowns in fast-moving environments
- Gaps in the skills of project participants
Lean methods assume a baseline of clarity and cooperation that rarely exists at the scale and complexity of today’s projects.
What Happens When Lean Isn’t Enough?
You’ve invested in Lean construction tools. Your team is holding planning sessions. Your schedules and checklists are in place. But the project still feels sluggish. Unfortunately, ensuring on-time, on-budget delivery while managing human coordination, uncertainty, and evolving challenges is difficult. That’s where relying solely on lean construction can fall short.
Here’s what we see when Lean falls short:
- Execution suffers despite thorough preplanning
- The project team hits delays caused by unclear decisions
- Meeting fatigue grows, but real alignment is missing
- Subcontractors follow the process, but outcomes don’t improve
Lean frameworks can make teams feel productive while critical misalignments go unresolved. This problem showed up in a recent Cleveland Clinic project, where Lean tools weren’t enough to solve the collaboration and communication challenges. The team needed something more. With three critical new projects on the horizon, the team knew they'd need a new approach to avoid the delays, cost overruns, and frustrations that were typical in the past. The solution required support at two levels.
First, the team implemented a new delivery model based on Integrated Project Delivery principles. Then, for each of the three sub-projects simultaneously being executed, a Senior Management Team, a Core Team, and a Project Execution Team were established for each. In the field, a robust Last Planner System was implemented for each project, including pull planning, weekly Work Planning, Make-Ready Planning, Daily Huddles, and tracking of PPC and variances.
As a result, all three builds were completed on time and within budget.
Download our Zero Punch List White Paper to learn more:
How the Midion Method Goes Beyond Lean
What is the Midion Method?
Over the last 25 years, the team at Midion has partnered on some of the most challenging projects and engaged in the most significant innovation conversations in construction and design. From these experiences, Midion has created a better way to work that inspires hope and promises a brighter future for the industry. It’s called the Midion Method.
The Midion Method was built to handle what Lean construction cannot: the people side of complex project management. It’s not about replacing Lean—it’s about expanding beyond it to make it work.
What makes the Midion Method different?
- Clarifies ownership. Define who owns what across companies and teams.
- Aligns stakeholders. Get decision-makers, builders, and planners on the same page.
- Builds durable communication rhythms. Move from vague meetings to structured, actionable dialogues.
- Adapts to complexity. Support systems evolve as the project does, without rigidity.
- Develops skills needed for team members to thrive together.
This isn’t theory. The Midion Method has been tested and proven on complex builds with multiple firms, tight timelines, and high stakes.
Discover the Midion Method:
Don’t Let Lean Construction Limit Your Project’s Potential
Lean is a great starting point. But it wasn’t designed to handle the real-world chaos, complexity, and communication needs of modern construction project management. If your project matters, and most do, don’t leave success to a toolset that stops short. Discover the Midion Method and equip your team with what Lean left out.
Let’s Talk About Your Project:
Why Lean Construction Can Leave You Stuck
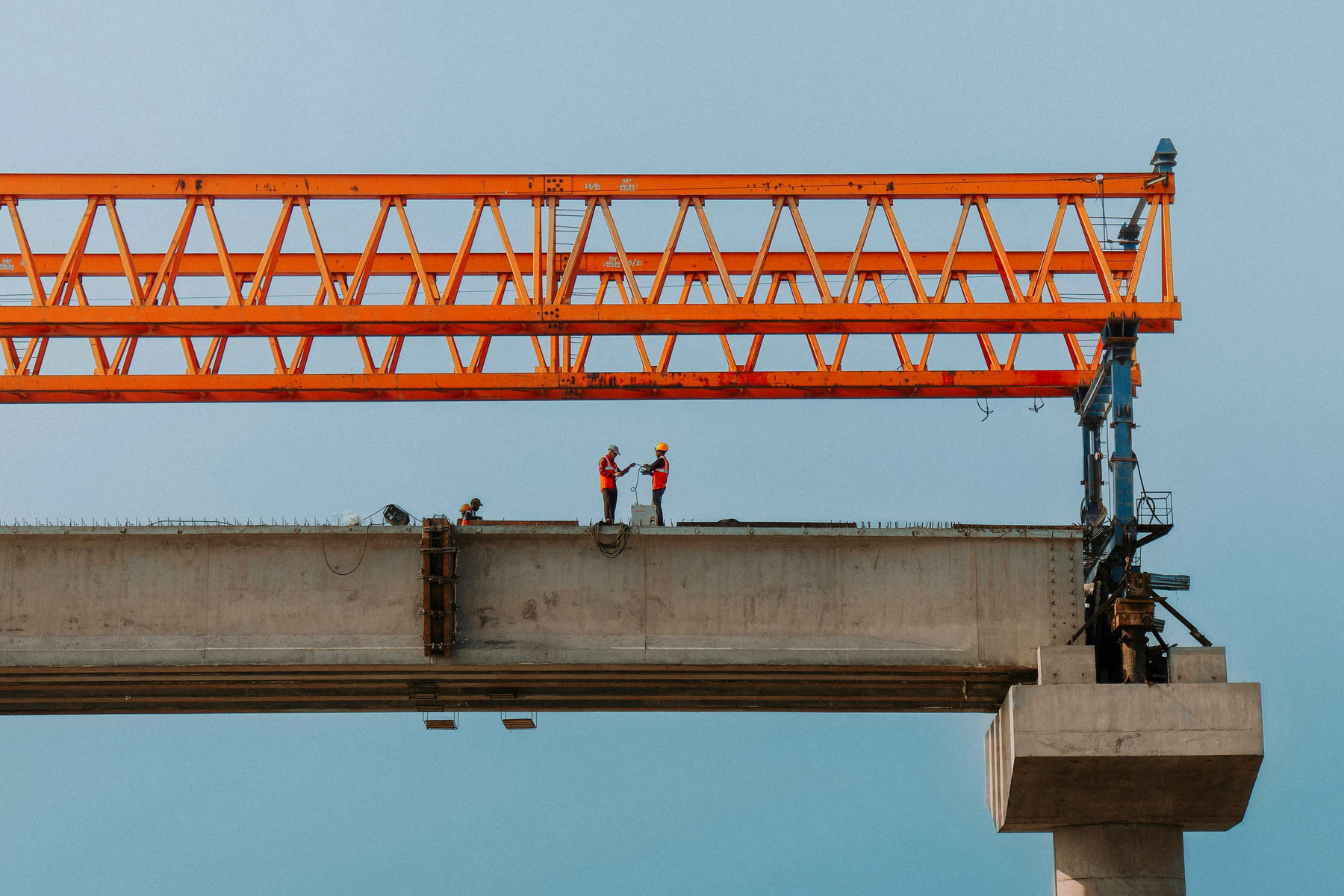
Lean construction has long been praised for boosting efficiency, cutting waste, and streamlining project delivery. And yes, it works…to a point. But if you’re managing complex construction projects with multiple stakeholders, shifting goals, and high stakes, Lean alone simply can’t address the deeper issues that derail progress.
Many teams still treat Lean as the ultimate solution. It’s not, and it might just leave you stuck.
Lean’s Limitations in Modern Construction Project Management
What is lean construction?
Lean construction is built around production-based thinking: reduce waste, improve flow, optimize processes. But today’s large-scale construction projects aren’t factories. They’re ecosystems of interdependent teams, layered decision-making, and evolving priorities.
Lean construction typically overlooks:
- Cross-organizational collaboration challenges
- Misaligned incentives between owners, designers, and contractors
- Ambiguity in leadership, decision-making, and accountability
- Communication breakdowns in fast-moving environments
- Gaps in the skills of project participants
Lean methods assume a baseline of clarity and cooperation that rarely exists at the scale and complexity of today’s projects.
What Happens When Lean Isn’t Enough?
You’ve invested in Lean construction tools. Your team is holding planning sessions. Your schedules and checklists are in place. But the project still feels sluggish. Unfortunately, ensuring on-time, on-budget delivery while managing human coordination, uncertainty, and evolving challenges is difficult. That’s where relying solely on lean construction can fall short.
Here’s what we see when Lean falls short:
- Execution suffers despite thorough preplanning
- The project team hits delays caused by unclear decisions
- Meeting fatigue grows, but real alignment is missing
- Subcontractors follow the process, but outcomes don’t improve
Lean frameworks can make teams feel productive while critical misalignments go unresolved. This problem showed up in a recent Cleveland Clinic project, where Lean tools weren’t enough to solve the collaboration and communication challenges. The team needed something more. With three critical new projects on the horizon, the team knew they'd need a new approach to avoid the delays, cost overruns, and frustrations that were typical in the past. The solution required support at two levels.
First, the team implemented a new delivery model based on Integrated Project Delivery principles. Then, for each of the three sub-projects simultaneously being executed, a Senior Management Team, a Core Team, and a Project Execution Team were established for each. In the field, a robust Last Planner System was implemented for each project, including pull planning, weekly Work Planning, Make-Ready Planning, Daily Huddles, and tracking of PPC and variances.
As a result, all three builds were completed on time and within budget.
Download our Zero Punch List White Paper to learn more:
How the Midion Method Goes Beyond Lean
What is the Midion Method?
Over the last 25 years, the team at Midion has partnered on some of the most challenging projects and engaged in the most significant innovation conversations in construction and design. From these experiences, Midion has created a better way to work that inspires hope and promises a brighter future for the industry. It’s called the Midion Method.
The Midion Method was built to handle what Lean construction cannot: the people side of complex project management. It’s not about replacing Lean—it’s about expanding beyond it to make it work.
What makes the Midion Method different?
- Clarifies ownership. Define who owns what across companies and teams.
- Aligns stakeholders. Get decision-makers, builders, and planners on the same page.
- Builds durable communication rhythms. Move from vague meetings to structured, actionable dialogues.
- Adapts to complexity. Support systems evolve as the project does, without rigidity.
- Develops skills needed for team members to thrive together.
This isn’t theory. The Midion Method has been tested and proven on complex builds with multiple firms, tight timelines, and high stakes.
Discover the Midion Method:
Don’t Let Lean Construction Limit Your Project’s Potential
Lean is a great starting point. But it wasn’t designed to handle the real-world chaos, complexity, and communication needs of modern construction project management. If your project matters, and most do, don’t leave success to a toolset that stops short. Discover the Midion Method and equip your team with what Lean left out.
Let’s Talk About Your Project:
Why Lean Construction Can Leave You Stuck
Why Lean Construction Can Leave You Stuck
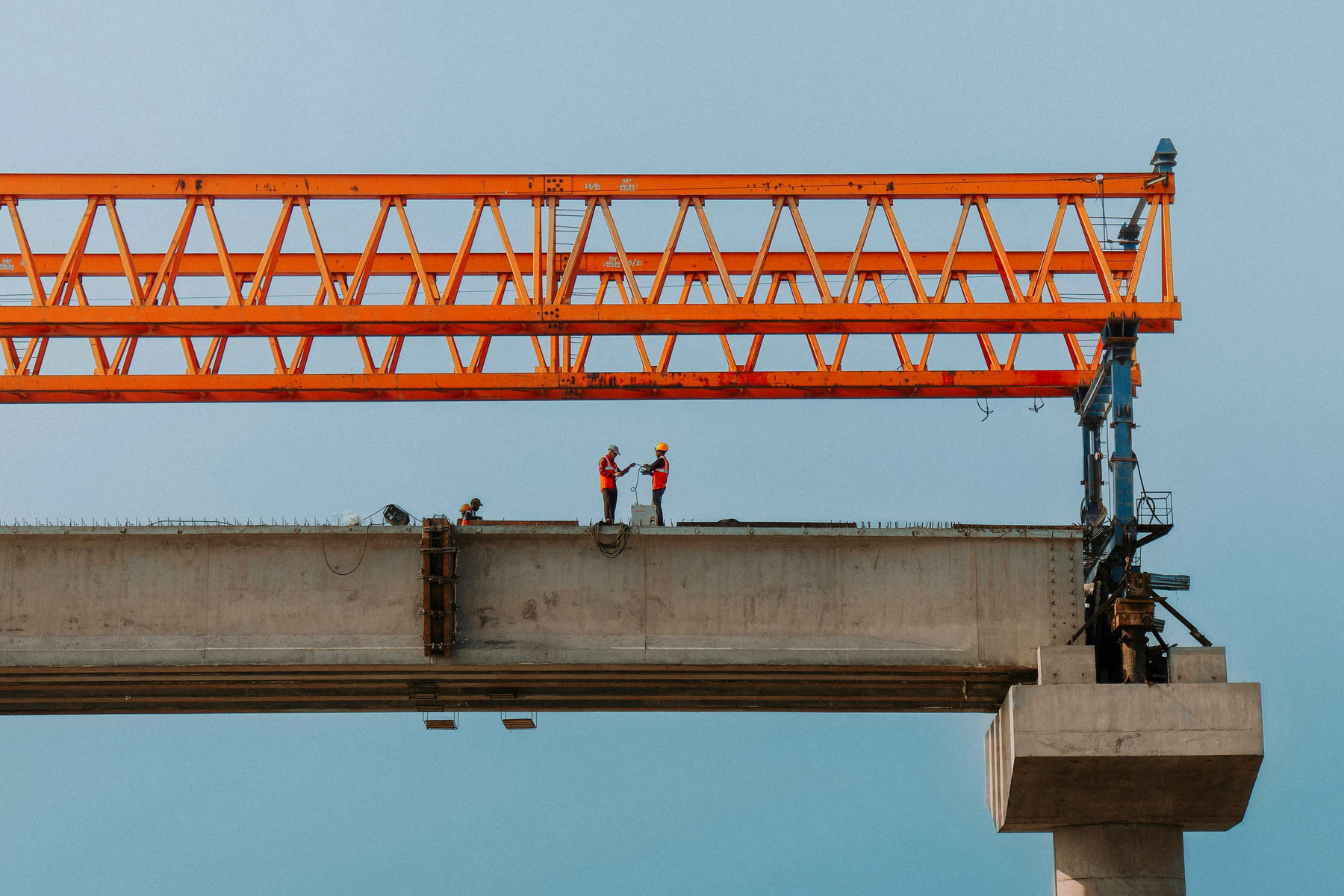
Lean construction has long been praised for boosting efficiency, cutting waste, and streamlining project delivery. And yes, it works…to a point. But if you’re managing complex construction projects with multiple stakeholders, shifting goals, and high stakes, Lean alone simply can’t address the deeper issues that derail progress.
Many teams still treat Lean as the ultimate solution. It’s not, and it might just leave you stuck.
Lean’s Limitations in Modern Construction Project Management
What is lean construction?
Lean construction is built around production-based thinking: reduce waste, improve flow, optimize processes. But today’s large-scale construction projects aren’t factories. They’re ecosystems of interdependent teams, layered decision-making, and evolving priorities.
Lean construction typically overlooks:
- Cross-organizational collaboration challenges
- Misaligned incentives between owners, designers, and contractors
- Ambiguity in leadership, decision-making, and accountability
- Communication breakdowns in fast-moving environments
- Gaps in the skills of project participants
Lean methods assume a baseline of clarity and cooperation that rarely exists at the scale and complexity of today’s projects.
What Happens When Lean Isn’t Enough?
You’ve invested in Lean construction tools. Your team is holding planning sessions. Your schedules and checklists are in place. But the project still feels sluggish. Unfortunately, ensuring on-time, on-budget delivery while managing human coordination, uncertainty, and evolving challenges is difficult. That’s where relying solely on lean construction can fall short.
Here’s what we see when Lean falls short:
- Execution suffers despite thorough preplanning
- The project team hits delays caused by unclear decisions
- Meeting fatigue grows, but real alignment is missing
- Subcontractors follow the process, but outcomes don’t improve
Lean frameworks can make teams feel productive while critical misalignments go unresolved. This problem showed up in a recent Cleveland Clinic project, where Lean tools weren’t enough to solve the collaboration and communication challenges. The team needed something more. With three critical new projects on the horizon, the team knew they'd need a new approach to avoid the delays, cost overruns, and frustrations that were typical in the past. The solution required support at two levels.
First, the team implemented a new delivery model based on Integrated Project Delivery principles. Then, for each of the three sub-projects simultaneously being executed, a Senior Management Team, a Core Team, and a Project Execution Team were established for each. In the field, a robust Last Planner System was implemented for each project, including pull planning, weekly Work Planning, Make-Ready Planning, Daily Huddles, and tracking of PPC and variances.
As a result, all three builds were completed on time and within budget.
Download our Zero Punch List White Paper to learn more:
How the Midion Method Goes Beyond Lean
What is the Midion Method?
Over the last 25 years, the team at Midion has partnered on some of the most challenging projects and engaged in the most significant innovation conversations in construction and design. From these experiences, Midion has created a better way to work that inspires hope and promises a brighter future for the industry. It’s called the Midion Method.
The Midion Method was built to handle what Lean construction cannot: the people side of complex project management. It’s not about replacing Lean—it’s about expanding beyond it to make it work.
What makes the Midion Method different?
- Clarifies ownership. Define who owns what across companies and teams.
- Aligns stakeholders. Get decision-makers, builders, and planners on the same page.
- Builds durable communication rhythms. Move from vague meetings to structured, actionable dialogues.
- Adapts to complexity. Support systems evolve as the project does, without rigidity.
- Develops skills needed for team members to thrive together.
This isn’t theory. The Midion Method has been tested and proven on complex builds with multiple firms, tight timelines, and high stakes.
Discover the Midion Method:
Don’t Let Lean Construction Limit Your Project’s Potential
Lean is a great starting point. But it wasn’t designed to handle the real-world chaos, complexity, and communication needs of modern construction project management. If your project matters, and most do, don’t leave success to a toolset that stops short. Discover the Midion Method and equip your team with what Lean left out.
Let’s Talk About Your Project:
Why Lean Construction Can Leave You Stuck
Why Lean Construction Can Leave You Stuck
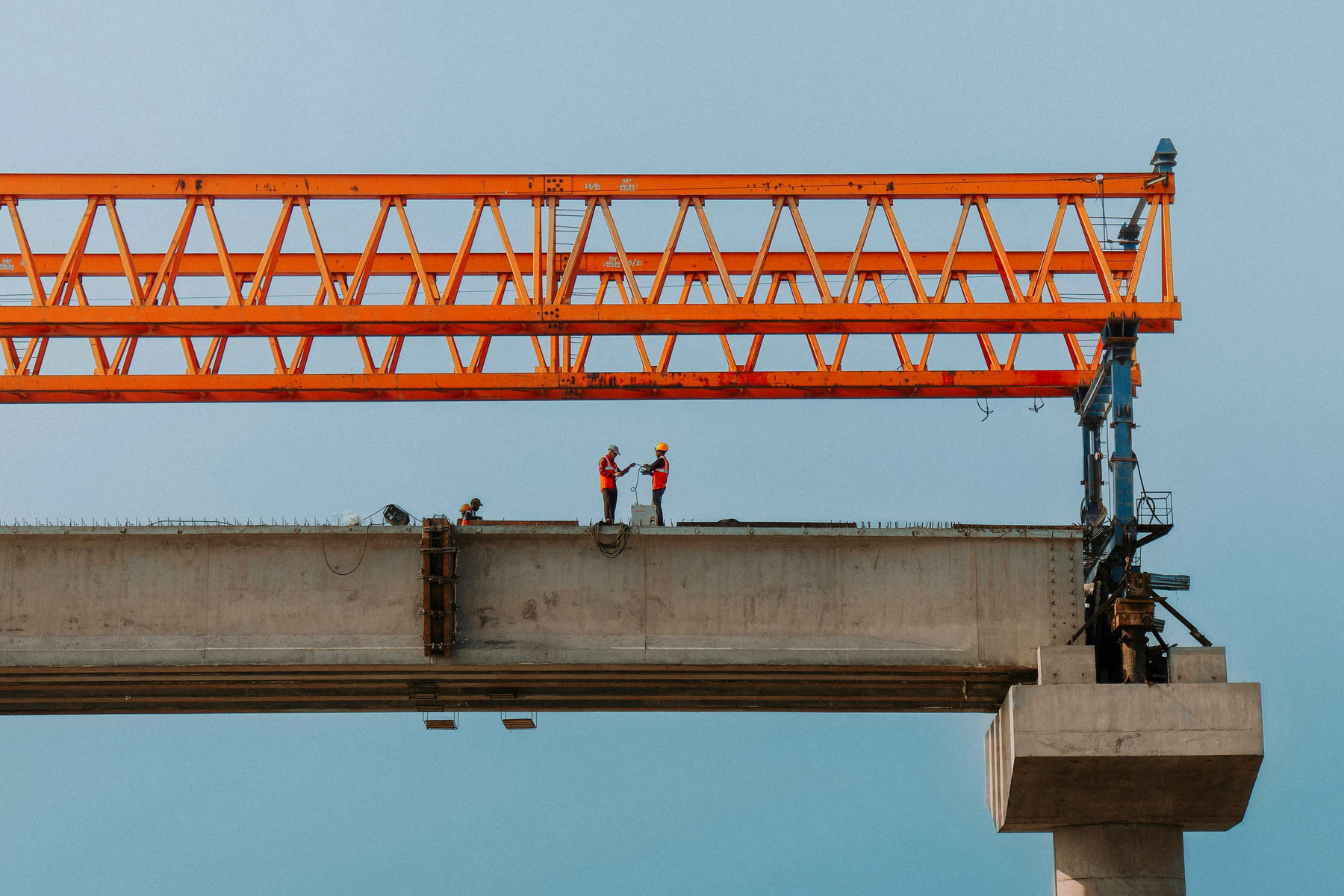
Lean construction has long been praised for boosting efficiency, cutting waste, and streamlining project delivery. And yes, it works…to a point. But if you’re managing complex construction projects with multiple stakeholders, shifting goals, and high stakes, Lean alone simply can’t address the deeper issues that derail progress.
Many teams still treat Lean as the ultimate solution. It’s not, and it might just leave you stuck.
Lean’s Limitations in Modern Construction Project Management
What is lean construction?
Lean construction is built around production-based thinking: reduce waste, improve flow, optimize processes. But today’s large-scale construction projects aren’t factories. They’re ecosystems of interdependent teams, layered decision-making, and evolving priorities.
Lean construction typically overlooks:
- Cross-organizational collaboration challenges
- Misaligned incentives between owners, designers, and contractors
- Ambiguity in leadership, decision-making, and accountability
- Communication breakdowns in fast-moving environments
- Gaps in the skills of project participants
Lean methods assume a baseline of clarity and cooperation that rarely exists at the scale and complexity of today’s projects.
What Happens When Lean Isn’t Enough?
You’ve invested in Lean construction tools. Your team is holding planning sessions. Your schedules and checklists are in place. But the project still feels sluggish. Unfortunately, ensuring on-time, on-budget delivery while managing human coordination, uncertainty, and evolving challenges is difficult. That’s where relying solely on lean construction can fall short.
Here’s what we see when Lean falls short:
- Execution suffers despite thorough preplanning
- The project team hits delays caused by unclear decisions
- Meeting fatigue grows, but real alignment is missing
- Subcontractors follow the process, but outcomes don’t improve
Lean frameworks can make teams feel productive while critical misalignments go unresolved. This problem showed up in a recent Cleveland Clinic project, where Lean tools weren’t enough to solve the collaboration and communication challenges. The team needed something more. With three critical new projects on the horizon, the team knew they'd need a new approach to avoid the delays, cost overruns, and frustrations that were typical in the past. The solution required support at two levels.
First, the team implemented a new delivery model based on Integrated Project Delivery principles. Then, for each of the three sub-projects simultaneously being executed, a Senior Management Team, a Core Team, and a Project Execution Team were established for each. In the field, a robust Last Planner System was implemented for each project, including pull planning, weekly Work Planning, Make-Ready Planning, Daily Huddles, and tracking of PPC and variances.
As a result, all three builds were completed on time and within budget.
Download our Zero Punch List White Paper to learn more:
How the Midion Method Goes Beyond Lean
What is the Midion Method?
Over the last 25 years, the team at Midion has partnered on some of the most challenging projects and engaged in the most significant innovation conversations in construction and design. From these experiences, Midion has created a better way to work that inspires hope and promises a brighter future for the industry. It’s called the Midion Method.
The Midion Method was built to handle what Lean construction cannot: the people side of complex project management. It’s not about replacing Lean—it’s about expanding beyond it to make it work.
What makes the Midion Method different?
- Clarifies ownership. Define who owns what across companies and teams.
- Aligns stakeholders. Get decision-makers, builders, and planners on the same page.
- Builds durable communication rhythms. Move from vague meetings to structured, actionable dialogues.
- Adapts to complexity. Support systems evolve as the project does, without rigidity.
- Develops skills needed for team members to thrive together.
This isn’t theory. The Midion Method has been tested and proven on complex builds with multiple firms, tight timelines, and high stakes.
Discover the Midion Method:
Don’t Let Lean Construction Limit Your Project’s Potential
Lean is a great starting point. But it wasn’t designed to handle the real-world chaos, complexity, and communication needs of modern construction project management. If your project matters, and most do, don’t leave success to a toolset that stops short. Discover the Midion Method and equip your team with what Lean left out.
Let’s Talk About Your Project:
Why Lean Construction Can Leave You Stuck
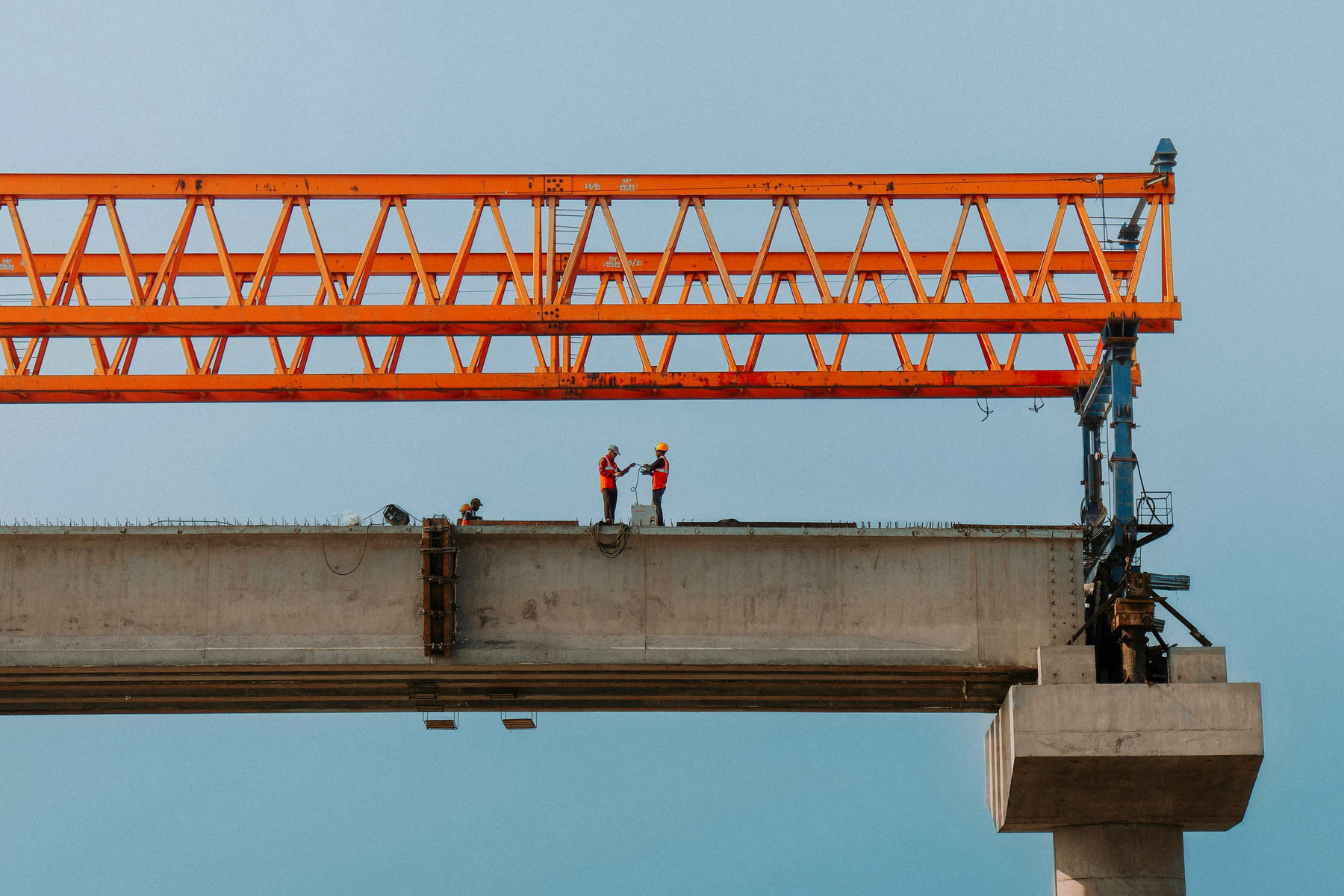
Lean construction has long been praised for boosting efficiency, cutting waste, and streamlining project delivery. And yes, it works…to a point. But if you’re managing complex construction projects with multiple stakeholders, shifting goals, and high stakes, Lean alone simply can’t address the deeper issues that derail progress.
Many teams still treat Lean as the ultimate solution. It’s not, and it might just leave you stuck.
Lean’s Limitations in Modern Construction Project Management
What is lean construction?
Lean construction is built around production-based thinking: reduce waste, improve flow, optimize processes. But today’s large-scale construction projects aren’t factories. They’re ecosystems of interdependent teams, layered decision-making, and evolving priorities.
Lean construction typically overlooks:
- Cross-organizational collaboration challenges
- Misaligned incentives between owners, designers, and contractors
- Ambiguity in leadership, decision-making, and accountability
- Communication breakdowns in fast-moving environments
- Gaps in the skills of project participants
Lean methods assume a baseline of clarity and cooperation that rarely exists at the scale and complexity of today’s projects.
What Happens When Lean Isn’t Enough?
You’ve invested in Lean construction tools. Your team is holding planning sessions. Your schedules and checklists are in place. But the project still feels sluggish. Unfortunately, ensuring on-time, on-budget delivery while managing human coordination, uncertainty, and evolving challenges is difficult. That’s where relying solely on lean construction can fall short.
Here’s what we see when Lean falls short:
- Execution suffers despite thorough preplanning
- The project team hits delays caused by unclear decisions
- Meeting fatigue grows, but real alignment is missing
- Subcontractors follow the process, but outcomes don’t improve
Lean frameworks can make teams feel productive while critical misalignments go unresolved. This problem showed up in a recent Cleveland Clinic project, where Lean tools weren’t enough to solve the collaboration and communication challenges. The team needed something more. With three critical new projects on the horizon, the team knew they'd need a new approach to avoid the delays, cost overruns, and frustrations that were typical in the past. The solution required support at two levels.
First, the team implemented a new delivery model based on Integrated Project Delivery principles. Then, for each of the three sub-projects simultaneously being executed, a Senior Management Team, a Core Team, and a Project Execution Team were established for each. In the field, a robust Last Planner System was implemented for each project, including pull planning, weekly Work Planning, Make-Ready Planning, Daily Huddles, and tracking of PPC and variances.
As a result, all three builds were completed on time and within budget.
Download our Zero Punch List White Paper to learn more:
How the Midion Method Goes Beyond Lean
What is the Midion Method?
Over the last 25 years, the team at Midion has partnered on some of the most challenging projects and engaged in the most significant innovation conversations in construction and design. From these experiences, Midion has created a better way to work that inspires hope and promises a brighter future for the industry. It’s called the Midion Method.
The Midion Method was built to handle what Lean construction cannot: the people side of complex project management. It’s not about replacing Lean—it’s about expanding beyond it to make it work.
What makes the Midion Method different?
- Clarifies ownership. Define who owns what across companies and teams.
- Aligns stakeholders. Get decision-makers, builders, and planners on the same page.
- Builds durable communication rhythms. Move from vague meetings to structured, actionable dialogues.
- Adapts to complexity. Support systems evolve as the project does, without rigidity.
- Develops skills needed for team members to thrive together.
This isn’t theory. The Midion Method has been tested and proven on complex builds with multiple firms, tight timelines, and high stakes.
Discover the Midion Method:
Don’t Let Lean Construction Limit Your Project’s Potential
Lean is a great starting point. But it wasn’t designed to handle the real-world chaos, complexity, and communication needs of modern construction project management. If your project matters, and most do, don’t leave success to a toolset that stops short. Discover the Midion Method and equip your team with what Lean left out.
Let’s Talk About Your Project:
Why Lean Construction Can Leave You Stuck
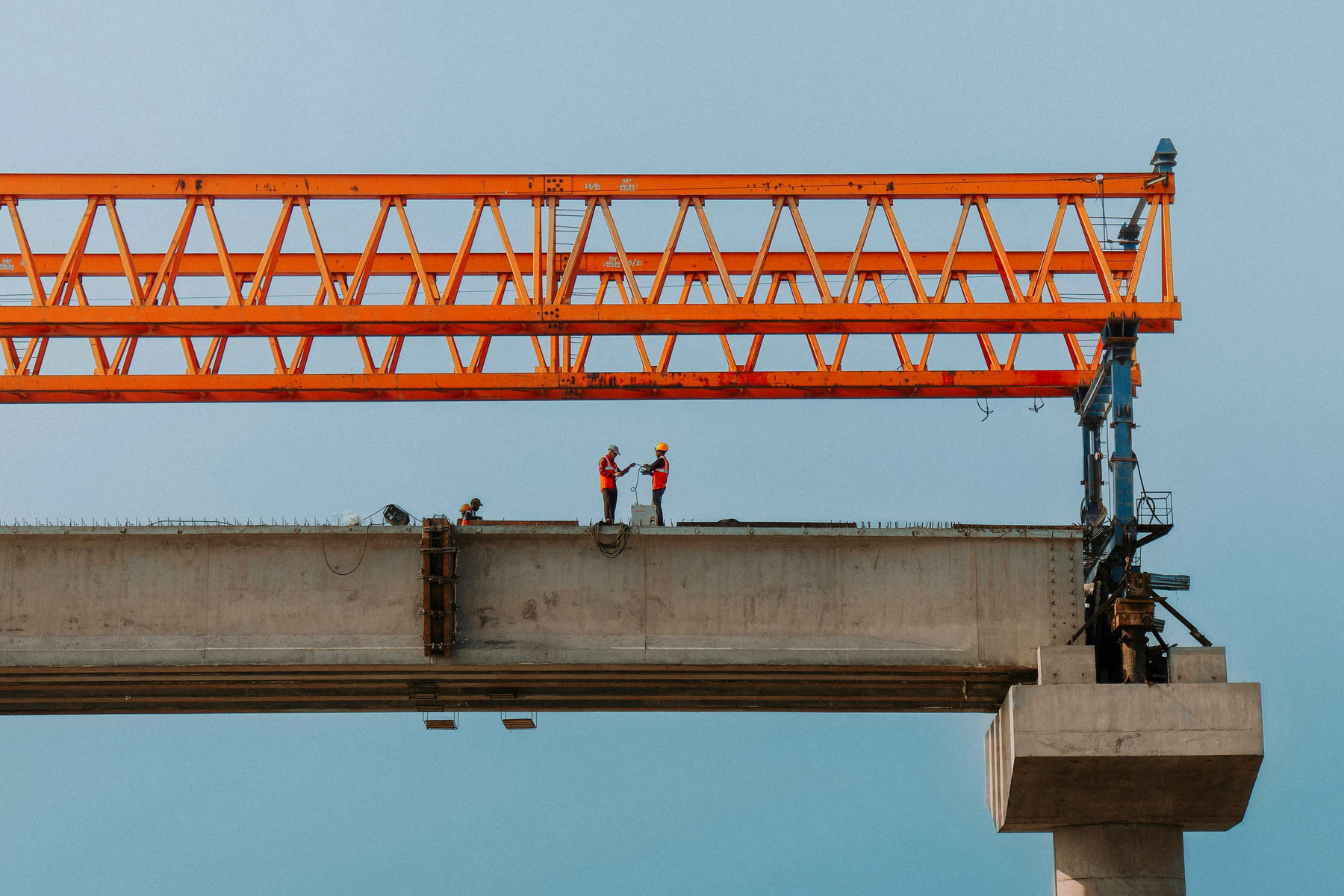
Lean construction has long been praised for boosting efficiency, cutting waste, and streamlining project delivery. And yes, it works…to a point. But if you’re managing complex construction projects with multiple stakeholders, shifting goals, and high stakes, Lean alone simply can’t address the deeper issues that derail progress.
Many teams still treat Lean as the ultimate solution. It’s not, and it might just leave you stuck.
Lean’s Limitations in Modern Construction Project Management
What is lean construction?
Lean construction is built around production-based thinking: reduce waste, improve flow, optimize processes. But today’s large-scale construction projects aren’t factories. They’re ecosystems of interdependent teams, layered decision-making, and evolving priorities.
Lean construction typically overlooks:
- Cross-organizational collaboration challenges
- Misaligned incentives between owners, designers, and contractors
- Ambiguity in leadership, decision-making, and accountability
- Communication breakdowns in fast-moving environments
- Gaps in the skills of project participants
Lean methods assume a baseline of clarity and cooperation that rarely exists at the scale and complexity of today’s projects.
What Happens When Lean Isn’t Enough?
You’ve invested in Lean construction tools. Your team is holding planning sessions. Your schedules and checklists are in place. But the project still feels sluggish. Unfortunately, ensuring on-time, on-budget delivery while managing human coordination, uncertainty, and evolving challenges is difficult. That’s where relying solely on lean construction can fall short.
Here’s what we see when Lean falls short:
- Execution suffers despite thorough preplanning
- The project team hits delays caused by unclear decisions
- Meeting fatigue grows, but real alignment is missing
- Subcontractors follow the process, but outcomes don’t improve
Lean frameworks can make teams feel productive while critical misalignments go unresolved. This problem showed up in a recent Cleveland Clinic project, where Lean tools weren’t enough to solve the collaboration and communication challenges. The team needed something more. With three critical new projects on the horizon, the team knew they'd need a new approach to avoid the delays, cost overruns, and frustrations that were typical in the past. The solution required support at two levels.
First, the team implemented a new delivery model based on Integrated Project Delivery principles. Then, for each of the three sub-projects simultaneously being executed, a Senior Management Team, a Core Team, and a Project Execution Team were established for each. In the field, a robust Last Planner System was implemented for each project, including pull planning, weekly Work Planning, Make-Ready Planning, Daily Huddles, and tracking of PPC and variances.
As a result, all three builds were completed on time and within budget.
Download our Zero Punch List White Paper to learn more:
How the Midion Method Goes Beyond Lean
What is the Midion Method?
Over the last 25 years, the team at Midion has partnered on some of the most challenging projects and engaged in the most significant innovation conversations in construction and design. From these experiences, Midion has created a better way to work that inspires hope and promises a brighter future for the industry. It’s called the Midion Method.
The Midion Method was built to handle what Lean construction cannot: the people side of complex project management. It’s not about replacing Lean—it’s about expanding beyond it to make it work.
What makes the Midion Method different?
- Clarifies ownership. Define who owns what across companies and teams.
- Aligns stakeholders. Get decision-makers, builders, and planners on the same page.
- Builds durable communication rhythms. Move from vague meetings to structured, actionable dialogues.
- Adapts to complexity. Support systems evolve as the project does, without rigidity.
- Develops skills needed for team members to thrive together.
This isn’t theory. The Midion Method has been tested and proven on complex builds with multiple firms, tight timelines, and high stakes.
Discover the Midion Method:
Don’t Let Lean Construction Limit Your Project’s Potential
Lean is a great starting point. But it wasn’t designed to handle the real-world chaos, complexity, and communication needs of modern construction project management. If your project matters, and most do, don’t leave success to a toolset that stops short. Discover the Midion Method and equip your team with what Lean left out.
Let’s Talk About Your Project:
Why Lean Construction Can Leave You Stuck
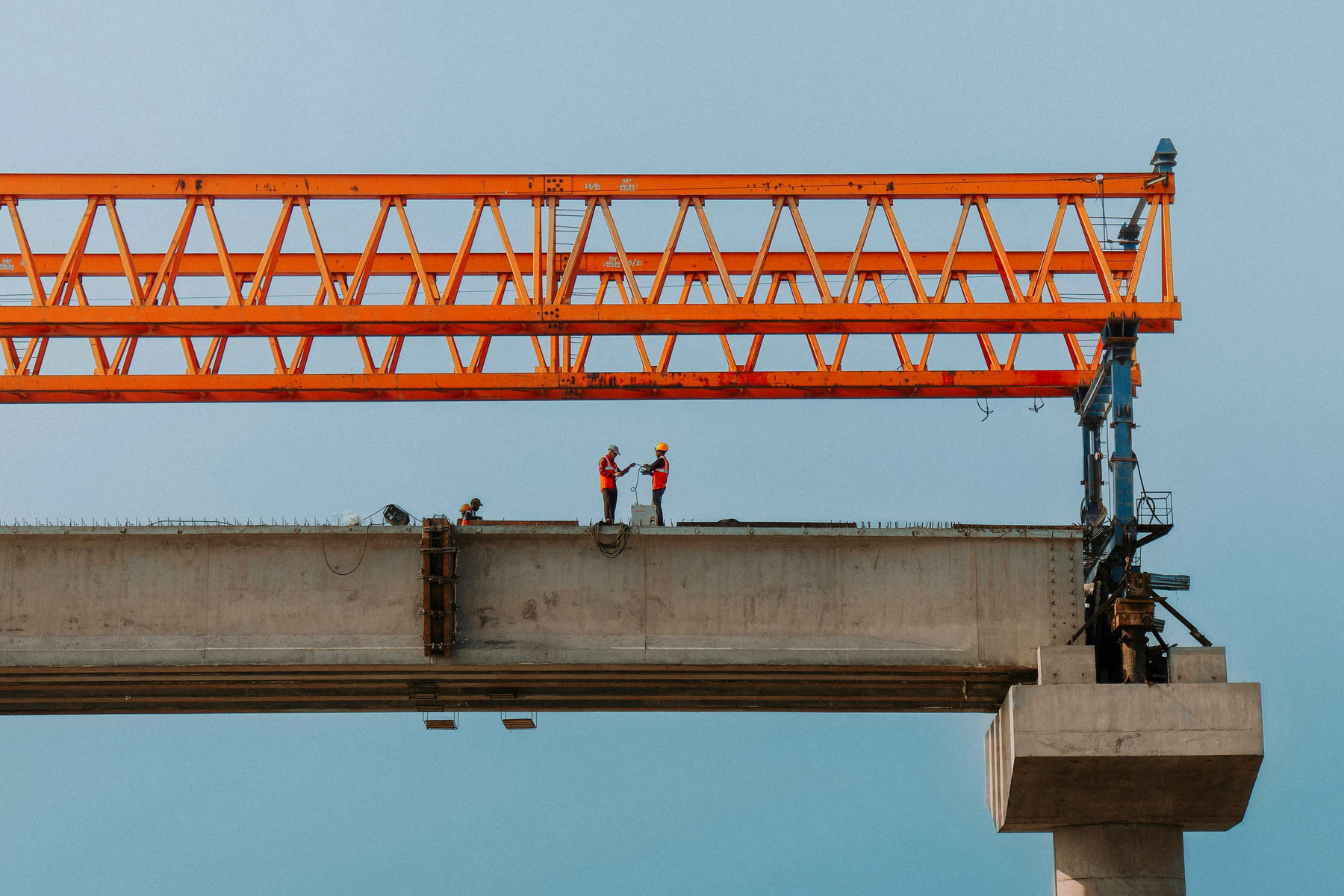
Lean construction has long been praised for boosting efficiency, cutting waste, and streamlining project delivery. And yes, it works…to a point. But if you’re managing complex construction projects with multiple stakeholders, shifting goals, and high stakes, Lean alone simply can’t address the deeper issues that derail progress.
Many teams still treat Lean as the ultimate solution. It’s not, and it might just leave you stuck.
Lean’s Limitations in Modern Construction Project Management
What is lean construction?
Lean construction is built around production-based thinking: reduce waste, improve flow, optimize processes. But today’s large-scale construction projects aren’t factories. They’re ecosystems of interdependent teams, layered decision-making, and evolving priorities.
Lean construction typically overlooks:
- Cross-organizational collaboration challenges
- Misaligned incentives between owners, designers, and contractors
- Ambiguity in leadership, decision-making, and accountability
- Communication breakdowns in fast-moving environments
- Gaps in the skills of project participants
Lean methods assume a baseline of clarity and cooperation that rarely exists at the scale and complexity of today’s projects.
What Happens When Lean Isn’t Enough?
You’ve invested in Lean construction tools. Your team is holding planning sessions. Your schedules and checklists are in place. But the project still feels sluggish. Unfortunately, ensuring on-time, on-budget delivery while managing human coordination, uncertainty, and evolving challenges is difficult. That’s where relying solely on lean construction can fall short.
Here’s what we see when Lean falls short:
- Execution suffers despite thorough preplanning
- The project team hits delays caused by unclear decisions
- Meeting fatigue grows, but real alignment is missing
- Subcontractors follow the process, but outcomes don’t improve
Lean frameworks can make teams feel productive while critical misalignments go unresolved. This problem showed up in a recent Cleveland Clinic project, where Lean tools weren’t enough to solve the collaboration and communication challenges. The team needed something more. With three critical new projects on the horizon, the team knew they'd need a new approach to avoid the delays, cost overruns, and frustrations that were typical in the past. The solution required support at two levels.
First, the team implemented a new delivery model based on Integrated Project Delivery principles. Then, for each of the three sub-projects simultaneously being executed, a Senior Management Team, a Core Team, and a Project Execution Team were established for each. In the field, a robust Last Planner System was implemented for each project, including pull planning, weekly Work Planning, Make-Ready Planning, Daily Huddles, and tracking of PPC and variances.
As a result, all three builds were completed on time and within budget.
Download our Zero Punch List White Paper to learn more:
How the Midion Method Goes Beyond Lean
What is the Midion Method?
Over the last 25 years, the team at Midion has partnered on some of the most challenging projects and engaged in the most significant innovation conversations in construction and design. From these experiences, Midion has created a better way to work that inspires hope and promises a brighter future for the industry. It’s called the Midion Method.
The Midion Method was built to handle what Lean construction cannot: the people side of complex project management. It’s not about replacing Lean—it’s about expanding beyond it to make it work.
What makes the Midion Method different?
- Clarifies ownership. Define who owns what across companies and teams.
- Aligns stakeholders. Get decision-makers, builders, and planners on the same page.
- Builds durable communication rhythms. Move from vague meetings to structured, actionable dialogues.
- Adapts to complexity. Support systems evolve as the project does, without rigidity.
- Develops skills needed for team members to thrive together.
This isn’t theory. The Midion Method has been tested and proven on complex builds with multiple firms, tight timelines, and high stakes.
Discover the Midion Method:
Don’t Let Lean Construction Limit Your Project’s Potential
Lean is a great starting point. But it wasn’t designed to handle the real-world chaos, complexity, and communication needs of modern construction project management. If your project matters, and most do, don’t leave success to a toolset that stops short. Discover the Midion Method and equip your team with what Lean left out.
Let’s Talk About Your Project: